Tool and Die
Precision Tooling, New Tooling, Adapting old tooling Tool for your impression die forging applications.
CAD/CAM Design
Before manufacturing of forging dies, we can not start the production process directly. Firstly, engineer need to know how to design the forging dies following the drawing of a new forging part. Design of forgings dies depends on the processing steps, nature of workpiece material, flow stress, working temperature, ect. All these factors need to be considered. Then engineers use CAD/CAM to draw it and make 3D models.
Die Manchining
After design of forging dies, we will start the manufacturing process. To obtain high precison, forging dies must be machined by CNC. So besides high material cost of forging dies, the machining cost is also quite high, that is why forging dies are much more expensive than casting moulds. And after finishing forging dies, we will forge several pieces of samples to check if the forging dies can be used in production.
Forging Die
Forging dies manufacturing is the first step to start a forging part. We all know that forging can be generally classified into two types, open die forging and closed die forging. Open die forging is operated between flat dies or dies in a simple shape. This process is mainly used for large parts. In closed die forging, metal billet is deformed in upper and lower dies for desired shape and dimensions.
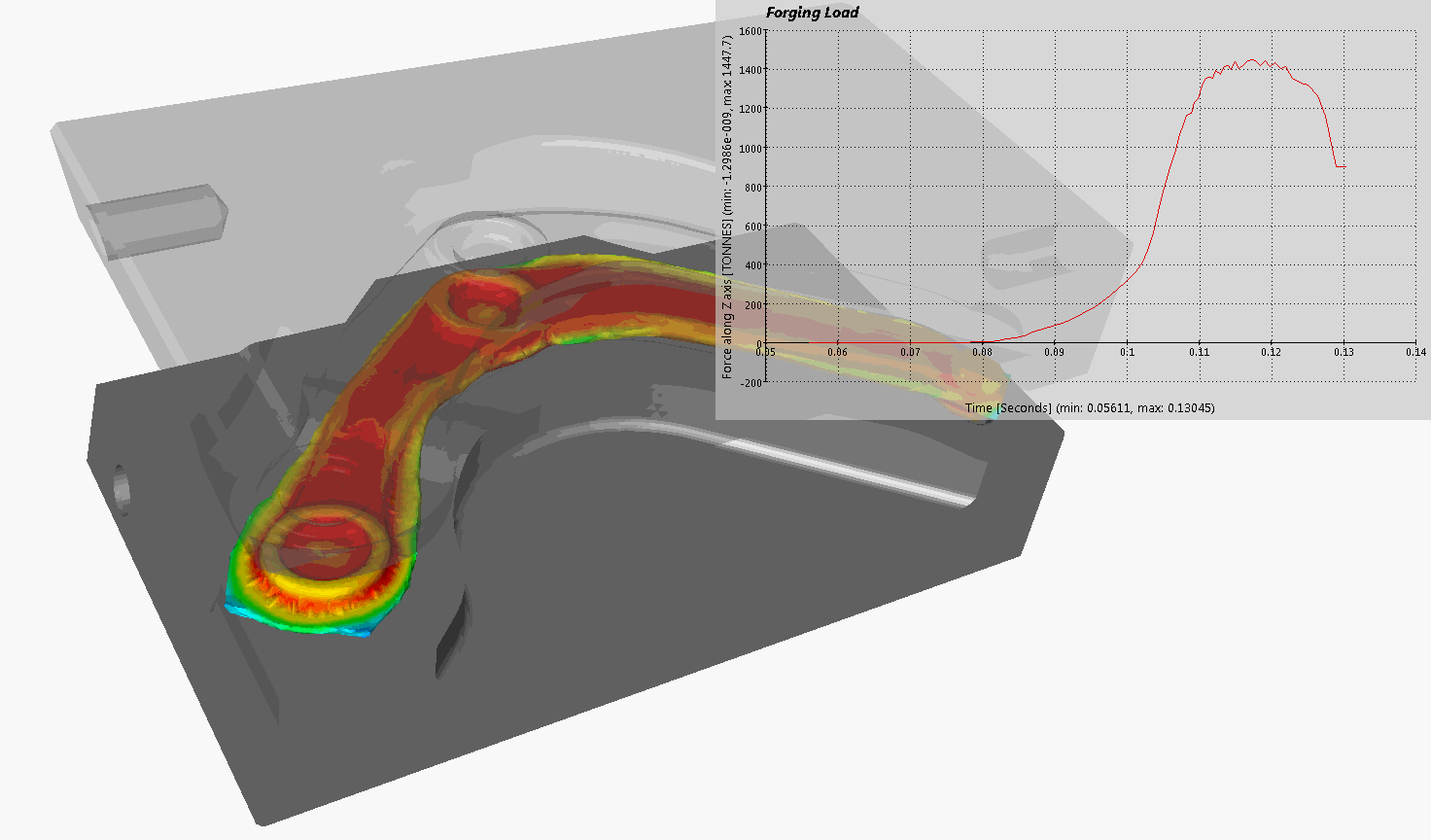
Manufacturing of Forging Tools & Dies
Forging dies manufacturing is the first step to start a forging part. We all know that forging can be generally classified into two types, open die forging and closed die forging. Open die forging is operated between flat dies or dies in a simple shape. This process is mainly used for large parts. In closed die forging, metal billet is deformed in upper and lower dies for desired shape and dimensions. Deformation occurs in the closed cavity under high pressures, which will achieve precision forgings with tight tolerances. So this process is widely used for the manufacture of simple as well as complex high strength precision parts, especially when safety factor is considered. As a closed die forging manufacturer, we would like to introduce the forging dies manufacturing for closed die forging parts in detail.
Before manufacturing of forging dies, we can not start the production process directly. Firstly,engineer need to know how to design the forging dies following the drawing of a new forging part. Design of forgings dies depends on the processing steps, nature of workpiece material, flow stress,working temperature,ect. All these factors need to be considered. Generally speaking, we need to calculate the volume of billet accurately to aviod under filling or excess filling. And selection of parting line(referring the lind where two dies meet) is also important. Sometimes for a forging part, there are several options to choose a parting line. And the best one is that the parting line can ensure the flow of material will be uniformly divided. In other words, forging is not feasible if there is no way to decide parting line, in this case, casting can be considered(see forging vs casting).
Another important point for forging dies manufacturing is the use of die material. Commonly used die materials are tool steels,high carbon high chromium die steels, ect. High die material cost will directly result in high forging dies cost. (For more detailed information, refer to select die material of closed die forging).
After design of forging dies, we will start the manufacturing process. To obtain high precison, forging dies must be machined by CNC. So besides high material cost of forging dies, the machining cost is also quite high, that is why forging dies are much more expensive than casting moulds. Normally a pair of forging dies will be 1500usd--3000usd. And for casting moulds, 600usd-1500usd is enough. And after finishing forging dies, we will forge several pieces of samples to check if the forging dies can be used in production. If forging defects are found, then we will still need to repair the dies until it can put into production perfectly. So as the largest forging supplier in China, we do not only equip with some large forging equipments to meet various demands of forgings, we also have our own mould workshop, so that we have the ability to make forging dies ourselves, which help our customers to save cost of forging dies, and meanwhile will greatly shorten the whole production time.
Our engineers use CAD/CAM to support the design of your component parts, and utilize in-house tool and die capabilities to support a wide range of impression die forgings and manufacturing processes. This includes Electrical Discharge Machining for production of precision tooling from EDM electrodes that are made in our shop.
Our techniques include process modeling and simulation, not only to provide confidence that the tool design provides defect free shaping, but also to predict the deformation process required for optimum metallurgical results. Guided by modeling and proven in tests of resulting forged product, we have provided customers with competitive advantages, allowing them to make performance guarantees unmatched by their peers.
Creating new tooling or adapting old forging tools to our production capabilities is an essential first step in meeting the tool and die requirements for setting up your job.
What is Forging Tooling & Dies?
In closed die forging, metal billets will be pressed in high pressure under upper and lower dies to get desired shaped. And then trimming with the workforce of punch machine to remove the flash. This is a trimming process using trimming dies. So you can see forging tooling is necessary for all custom steel forgings in closed die forging process.
The strength of the tooling or dies for steel forgings must be much higher than steel forging materials. So common selected material of forging dies are tool steel, such as H13. In casting, for its pouring process, aluminum tooling is enough. So material cost of forging dies are higher than that of casting molds.
For the simplest shaped steel forgings, normally the tooling required is: forging dies and trimming dies. But for some thin wall products, the product might be easy deformed after forging or heat treatment. To ensure correct dimensions and tolerances, extra flatten die will be needed. However, in casting, just a pair of molds is enough. This is another reason why forging dies are much more expensive.
Tooling Cost for Steel Forging
Tooling cost is calculated according to the structure and dimensions of steel forgings. Normally, for a simple forged product less than 5kg, we may charge 2000-3000usd. But for large parts, or thin wall thickness parts, the tooling cost will be increased for added tool material or flatten dies.
So in quotation stage, we will send us our customer a offical quotation including tooling cost and unit cost.
If our company designed, engineered, and manufactured the tooling for your steel forging project, we will maintain that tooling at no additional charge for the life of the part. If the tooling wears out, breaks, or is otherwise damaged, we will repair and maintain it in ideal working condition for as long as you continue to contract with us for part forging.
In-house Tool & Die Capabilities
As professional steel forging company, CHISEN has its own tool and die shop, and one of our core competencies is that we can develop and maintain the tool and die for steel forgings ourselves. We can develop precision tooling and dies to forge almost any part at net or near-net shape in precise tolerances. All tooling is custom made at our tooling facility, which helps us ensure the quality and accuracy of our tooling and reduces tooling costs.
We recently built a world class, climate controlled tool and die shop. Our vast in-house tooling manufacturing capabilities ensure quick turnaround of any custom-forged production runs. We produce 100% of our own die requirements internally through the use of CNC high speed mills checked by CMM.