Metal Forging
Metal forging is a metal forming process that involves applying compressive forces to a work piece to deform it, and create a desired geometric change to the material. The forging process is very important in industrial metal manufacture, particularly in the extensive iron and steel manufacturing industry.
Metal Forging
Metal forging is a metal forming process that involves applying compressive forces to a work piece to deform it, and create a desired geometric change to the material. The forging process is very important in industrial metal manufacture, particularly in the extensive iron and steel manufacturing industry. A steel forge is often a source of great output and productivity. Work stock is input to the forge, it may be rolled, it may also come directly from cast ingots or continuous castings. The forge will then manufacture steel forgings of desired geometry and specific material properties. These material properties are often greatly improved.
Metal forging is known to produce some of the strongest manufactured parts compared to other metal manufacturing processes, and obviously, is not just limited to iron and steel forging but to other metals as well. Different types of metals will have a different factors involved when forging them, some will be easier to forge than others. Various tests are described latter to determine forging process factors for different materials. Aluminum, magnesium, copper, titanium, and nickel alloys are also commonly forged metals. It is important to understand the principles of manufacturing forged products, including different techniques and basic metal forging design. The following will provide a comprehensive overview of the metal forging process.
Metal forging, specifically, can strengthen the material by sealing cracks and closing empty spaces within the metal. The hot forging process will highly reduce or eliminate inclusions in the forged part by breaking up impurities and redistributing their material throughout the metal work. However, controlling the bulk of impurities in the metal should be a consideration of the earlier casting process. Inclusions can cause stress points in the manufactured product, something to be avoided. Forging a metal will also alter the metal's grain structure with respect to the flow of the material during its deformation, and like other forming processes, can be used to create favorable grain structure in a material greatly increasing the strength of forged parts. For these reasons, metal forging manufacture gives distinct advantages in the mechanical properties of work produced, over that of parts manufactured by other processes such as only casting or machining.
Metal forgings can be small parts, or weigh as much as 700,000 lbs. Products manufactured by forging in modern industry include critical aircraft parts such as landing gear, shafts for jet engines and turbines, structural components for transportation equipment such as automobiles and railroads, crankshafts, levers, gears, connecting rods, hand tools such as chisels, rivets, screws, and bolts to name a few. The manufacture of forging die and the other high costs of setting up an operation make the production of small quantities of forged parts expensive on a price per unit basis. Once set up, however, operation costs for forging manufacture can be relatively low, and many parts of the process may be automated. These factors make manufacturing large quantities of metal forgings economically beneficial.
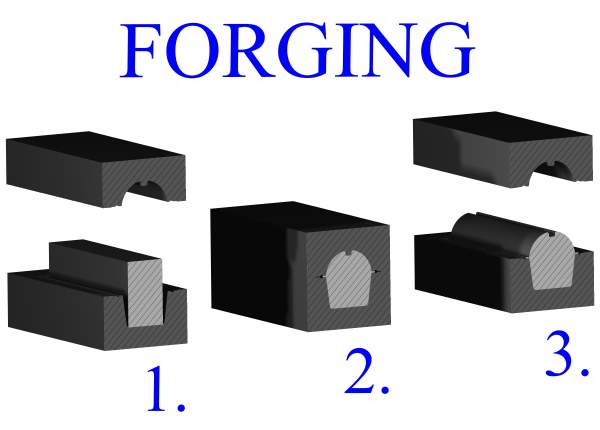
Hot Die Vs. Cold Die Forging
Most metal forging operations are carried out hot, due to the need to produce large amounts of plastic deformation in the part, and the advantage of an increased ductility and reduced strength of the work material. Hot die forging also eliminates the problem of strain hardening the metal. In cases where it is desirable to create a favorable strain hardening of the part, cold die forging may be employed. Cold die forging manufacture, while requiring higher forces, will also produce greater surface finish and dimensional accuracy than hot die forging. Some specific metal forging processes are always performed cold, such as coining.
Classification Of Metal Forging Processes
Metal forging processes can be classified by the degree to which the flow of material is constrained during the process. There are three major classifications in metal forging manufacture. First, open die forging, in which the work is compressed between two die that do not constrain the metal during the process. Secondly, impression die forging, in which cavities within the die restrict metal flow during the compression of the part, causing the material to deform into a desired geometric shape. Some material in impression die forging is not constrained by the cavities and flows outward from the die, this metal is called flash. In industrial metal forging, a subsequent trimming operation will be performed to remove the flash. The third type of metal forging is flashless forging. In flashless forging manufacture the entire work piece is contained within the die in such a way that no metal can flow out of the die cavity during the compression of the part, hence no flash is produced.
Open Die Forging
The manufacturing process of metal forging has been performed for at least 7,000 years, perhaps even 10,000 years. The most basic type of forging would have been shaping some metal by striking it with a rock. Latter the employment of different materials, such as bronze then iron and steel, and the need for forged metal products such as swords and armor, led way to the art of blacksmithing or blacksmith forging. Blacksmithing is an open die forging process where the hammer and anvil surfaces serve as opposing flat die. Bronze forgings, followed by iron and steel forgings, mark some of man's earlier manufacturing prowess.
A simple type of open die forging is called upsetting. In an upsetting process the work is placed between two flat die and its height is decreased by compressive forces exerted between the two die. Since the volume of a metal will remain constant throughout its deformation, a reduction in height will be accompanied by an increase in width. Figure 155 shows a flat die upsetting process, under ideal conditions.
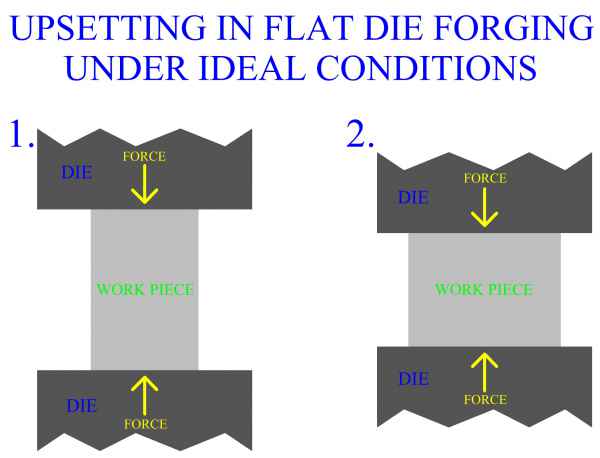
In real conditions during industrial manufacturing, friction plays a part in the process. Friction forces at the die-work interface oppose the spreading of the material near the surfaces, while the material in the center can expand more easily. The result is to create a barrel shape to the part. This effect is called barreling in in metal forging terms. Barreling is generally undesirable and can be controlled by the use of effective lubrication. Another consideration, during hot forging manufacture, that would act to increase the barreling effect would be the heat transfer between the hot metal and the cooler die. The metal nearer to the die surfaces will cool faster than the metal towards the center of the part. The cooler material is more resistant to deformation and will expand less than the hotter material in the center, also causing a barreling effect.
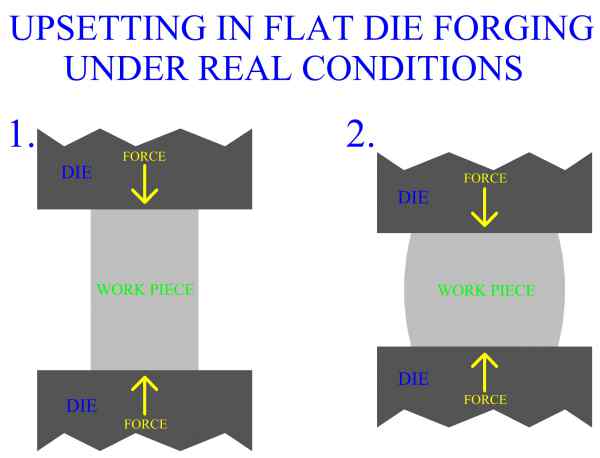
Another common open die forging process performed in industrial metal forging manufacture, involves using flat die to round an ingot. With the use of mechanical manipulators, a work piece is compressed and rotated in a series of steps eventually forming the metal into a cylindrical part. The compressions affect the material of the forging, closing up holes and gaps, breaking down and reforming weak grain boundaries, and creating a wrought grain structure. As this open die forging process progresses the material of the part will be altered from the outside first, progressing inward. It is important that when manufacturing a metal forging by this process, the part is worked significantly enough to change the structure of the material in the center of the work piece. Large shafts for motors and turbines are forged this way from cast ingots.
Cogging, or drawing out, is often used in manufacturing industry. Cogging is an open die forging process in which flat or slightly contoured die are employed to compress a work piece, reducing its thickness and increasing its length. In a cogging operation, the forging is large relative to the size of the die. The part is forged in a series of steps. After each compression of the material, the open die advance along the length of the work piece and perform another forging compression. The distance the die travel forward on the work piece between each forging step is called the bite, and is usually about 40 to 75 percent of the width of the die, in industrial practice. A greater reduction in the thickness of the forged part can be accomplished by decreasing the width of the bite. Cogging allows for smaller machinery with less power and forces to form work of great length. Often in commercial manufacture of metal products, cogging may be just one metal forging process in a series of metal forging processes required to form a desired part. Sometimes formed products such as metal fences may be produced directly from cogging.
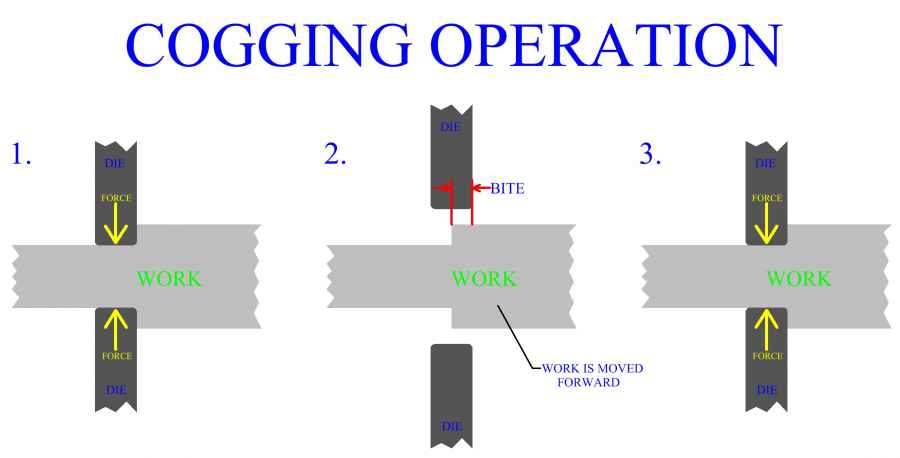
A typical open die forging process performed in metal forging manufacture is fullering. Fullering is mostly used as an earlier step to help distribute the material of the work in preparation for further metal forging operations. This often occurs when a manufacturing process requires several forging operations to complete. The metal forging process design section will discuss this concept later. In fullering, open die with convex surfaces are used to deform the work piece. The result is to cause metal to flow out of one area and to both sides.
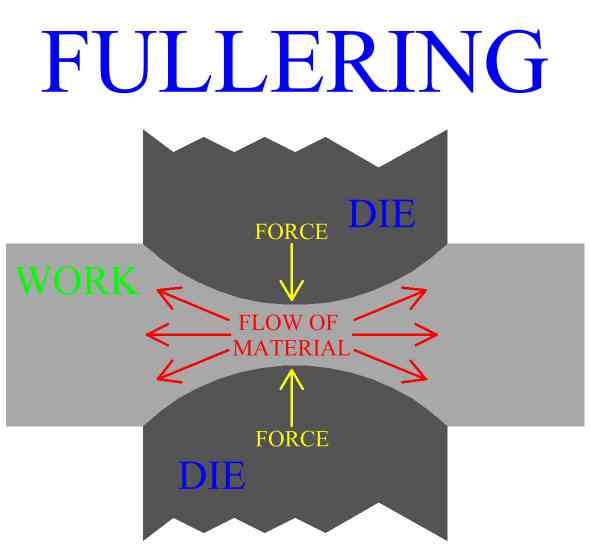
Edging is also an open die forging process often used in manufacturing practice, to prepare a work for sequential metal forging processes. In edging, open die with concave surfaces plastically deform the work material. Edging acts to cause metal to flow into an area from both sides. Edging and fullering both are used to redistribute bulk quantities of the metal forging's material.
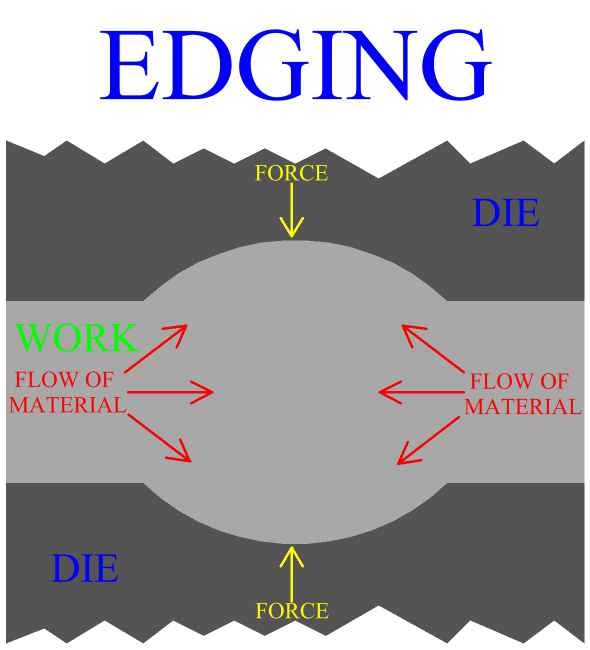
Impression Die Forging
Impression die forging manufacture involves compression of a work piece by the use of impression die, (a mold), that contain cavities that act to restrict the flow of metal within the die during the deformation of the work. The metal will fill the space within the die cavity as it is plastically compressed into the mold. Closing of the mold completes the deformation, hence impression die forging is also referred to as closed die forging. The forged metal part will now have the geometric dimensions of the mold, provided a complete filling of the die cavity occurred during the process. The operation of forcing metal to flow into and fill the impressions in the die will also alter the grain structure of the metal. The creation of favorable grain structure through controlled material deformation should always be a consideration in the design of an impression die forging process.
One characteristic of impression die forging manufacture is the formation of flash or fin around the forged part. During the design of the metal forging operation, the volume of the starting work piece is made slightly higher than that of the closed die cavity. As the die close, and the work metal flows into and fills the contours of the impression, some excess material will flow out of the die and into the area between the two die. This will form a thin plane of metal all around the work at the parting line, (where the two die meet when they close), of the forged product. Flash is trimmed from the forging in a latter process.
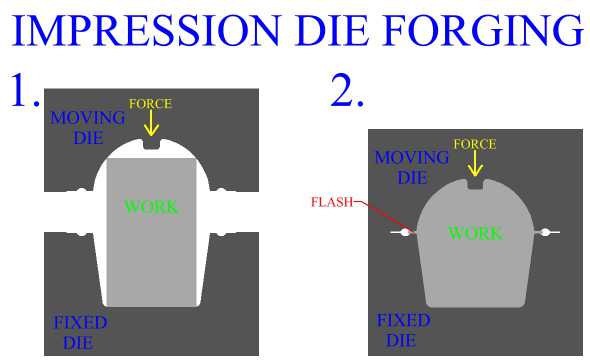
Precision Forging
Modern technological advances in the metal forging process and in the design of die, have allowed for the development of precision forging. Precision forging may produce some or no flash and the forged metal part will be at or near its final dimensions, requiring little or no finishing. The number of manufacturing operations is reduced as well as the material wasted. In addition, precision forging can manufacture more complex parts with thinner sections, reduced draft angles, and closer tolerances. The disadvantages of these advanced forging methods are that special machinery and die are needed, also more careful control of the manufacturing process is required. In precision forging, the amount of material in the work, as well as the flow of that material through the mold must be accurately determined. Other factors in the process such as the positioning of the work piece in the cavity must also be performed precisely.
Flashless Forging
Flashless forging is a type of precision forging process in which the entire volume of the work metal is contained within the die and no material is allowed to escape during the operation. Since no material can leave the mold as the part is forged, no flash is formed. Like other precision forging processes, flashless forging has rigorous process control demands, particularly in the amount of material to be used in the work piece. Too little material and the die will not fill completely, too much material will cause a dangerous build up of forces.
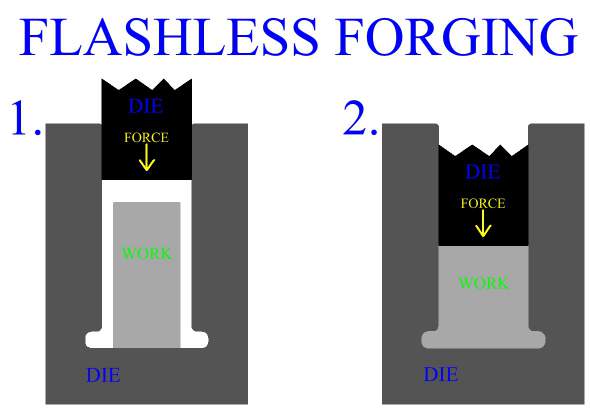
Metal Forgeability
Metal selection must be considered carefully in forging manufacture. The ability of a metal to experience deformation without failure or cracking is an important characteristic to consider in its selection as a material for a forging process. In metal forging industry, several tests have been developed to try and quantify this ability. The amount of deformation a particular metal can tolerate without failure is directly related to that metal's forgeability. The higher the amount of deformation, the higher the forgeability.
One popular test involves compressing a cylindrical work stock between two flat die. This is called upsetting the work, thus this test is called the upsetting test. In an upsetting test, the work stock is compressed by flat open die, reducing the work in height until cracks form. The amount of reduction can be considered a measurement of forgeability. Upsetting tests can be performed at different temperatures and different compression speeds. Testing various temperatures and strain rates will help determine the best conditions for the forging of a particular metal.
Another common test used in modern industry is called the hot twist test. In a hot twist test, a round bar is twisted in one direction until material failure occurs. The amount of rotation is taken as a quantitative measurement of metal forgeability. This test is often conducted on a material at several different temperatures. Other tests are also used in industrial metal forging manufacture. Impact testing is sometimes used to gauge the forgeability of a material. Cracks in the metal are the common criteria for failure for most tests, however, forgeability tests can also determine other negative effects that a material may exhibit under different conditions of stress, strain rate, and temperature.
Defects In Metal Forging
Inspection is an important aspect of metal forging manufacture. All parts should be checked for defects after the manufacturing process is complete. Defects of metal forged product include exterior cracking, interior cracking, laps, cold shuts, warping of the part, improperly formed sections and dead zones. Cracking both interior and exterior is caused by excessive stress, or improper stress distribution as the part is being formed. Cracking of a forging can be the result of poorly designed forging die or excess material in the work piece. Cracks can also be caused by disproportionate temperature distributions during the manufacturing operation. High thermal gradients can cause cracks in a forged part.
Laps or folds in a metal forging are caused by a buckling of the part, laps can be a result of too little material in the work piece. Cold shuts occur when metal flows of different temperatures meet, they do not combine smoothly, a boundary layer, (cold shut), forms at their intersection. Cold shuts indicate that there is a problem with metal flow in the mold as the part is being formed. Warping of a forged part can happen when thinner sections cool faster than the rest of the forging. Improperly formed sections and dead zones can be a result of too little metal in the work piece or flawed forging die design resulting in incorrect material distribution during the process.
In general, defects in parts manufactured by metal forging can be controlled first by careful consideration of work stock volume, and by good design of both the forging die, (mold), and the process. The main principle is to enact the right material distributions, and the right material flow to accomplish these distributions. Die cavity geometry and corner radius play a large roll in the action of the metal. Forging die design, and forging process design will be discussed in later sections.
Lubrication In Industrial Metal Forging Manufacture
Frictional forces within the mold, between the work and the surfaces of the die cavity, have a large influence over the flow of material in a metal forging operation. Lubricants are used in industrial metal forging production in order to lower frictional forces, and enact a smoother flow of metal through the mold. In addition, they are used to slow the cooling of the work and reduce temperature gradients, in hot forging manufacture, serving as a thermal barrier between the metal work and the die. Lubricants also help keep the metal and die surfaces from sticking together and assist in the removal of the metal forging from the die. Common lubricants used in modern forging industry include, water, mineral oil, soap, saw dust, graphite, molybdenum disulfide, and liquid glass.
Forging Die Material
The exact material used to make a forging die,(mold), is dependant upon all the details of that particular metal forging process. In general, a forging die must be tough, possess high strength and hardness at elevated temperatures, good shock resistance, resistance to thermal gradients, hardenability and ability to withstand abrasive wear. During the manufacture of a hot forged part, the forging die is usually preheated before the operation begins. Preheating forging die reduces thermal cycling that can cause cracks in the die.
Metal forging die are hardened and tempered. Forging die dimensions must account for shrinkage of the work, as well as extra material allowances for the finishing of the part. The abrasive wear present in hot forging operations is due largely to the scale on the work stock. Much of the scale can be removed from the blank immediately after heating in the furnace, prior to the forging of the part. Adequate lubrication can also greatly mitigate wear. Sometimes a forging die may be assembled using different die sections. These sections, called die inserts, are manufactured separately and may be of different materials. Complex cavities can be produced easier with die inserts, also different sections of the forging die can be individually replaced.
Some factors to consider when determining the material composition of a forging die are, type of operation, number of die forgings, size of forged parts, complexity of forged parts, type of machinery to be used, temperature that the metal will be forged at, and the cost of materials. Forging die are made from tool steels that, depending upon process criteria, are alloyed with various levels of one or more of these materials, chromium, molybdenum, vanadium, and nickel. Die blocks are cast from the alloy, forged themselves, then machined, and finished.
Forging Die Design
Forging die design will always depend on the factors and requirements of the manufacturing process. However, there are some general principles to consider for good forging die design. During the forging process metal is flowing under pressure to fill the impression within the die cavity, (mold). Similar to the metal casting process of die casting, in metal forging, an increase in pressure on the metal within the die will increase the ability to fill the die cavity completely. One main difference between the processes is that in die casting the metal is liquid, while in forging the work is a solid metal above or below its recrystallization temperature. Smaller, thinner, longer, and more complex sections can be produced with more pressure, but too much pressure within the die cavity is bad because it can damage the die and machinery.
The formation of metal flash is an important part of impression die forging manufacture. First, flash provides a way for excess material from the work stock to exit the forging die. If this material could not escape during the compression the build up of pressure, as the volume of work metal exceeded the volume of the die cavity, could easily crack the die. Flash, while allowing material to escape, does increase the pressure within the die cavity. Flash must travel through a narrow passage, called land, before it opens up into a gutter.
As it flows through land, the friction between the metal flash and the mating surfaces resists further flow of material out of the die cavity, increasing pressure within the forging die. In addition, the cooling of the flash from the mating surfaces increases resistance to flow of material out of the die, thus also increasing pressure within the die cavity. A longer land will cause the metal flash to have to flow further under resistance, increasing the die pressure. Decreasing the width of land will also increase pressure within the forging die by increasing the cooling rate of the flash, as the temperature goes down the metal's resistance to flow goes up. More resistance to metal flow will cause a thinner land to create higher die pressure. The pressure within the forging's die cavity is often controlled by varying the width of land.
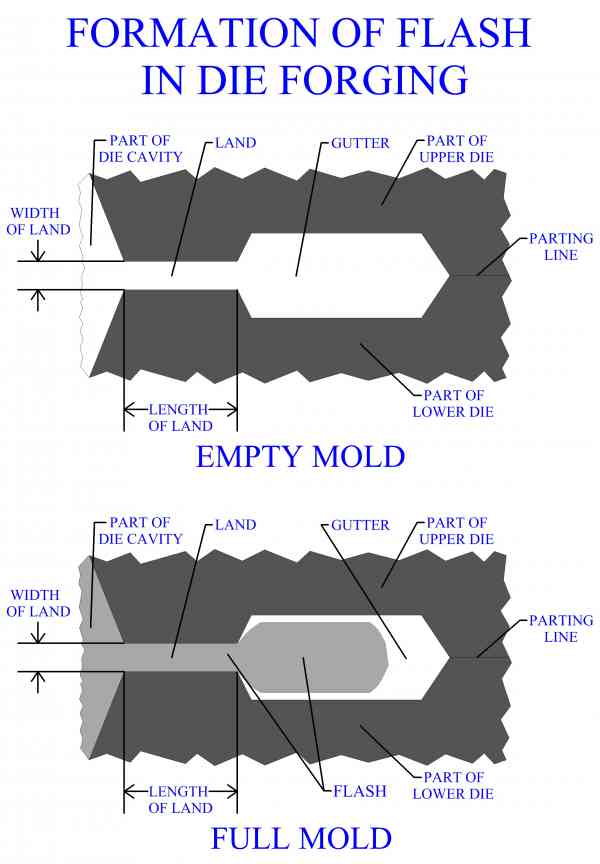
One of the main principles to remember when designing a forging die for a specific manufacturing process is that while deformation of the metal is occurring, the material will tend to flow in the direction of least resistance. Proper metal flow within the die is important in ensuring a complete filling of the die cavity, preventing defects, and in controlling the grain structure of the forged part. Friction in the die is an important consideration in metal forging manufacture. Friction will act to resist the movement of the material and increase the forces required to fill the die cavity during the process. More forces, in turn, mean more stress and wear on the mold and equipment.
Another critical factor in the movement of material within the die cavity during the forming of the part, is the interior geometry of the die cavity. The size of the forged part, work material, complexity of the forged part, size and thickness of different part features, and distance different areas are from the parting line, are some of the important factors concerning the structure of the forging die. Basically thinner more complex features will be more difficult to fill completely, as would areas further from the parting line or out of the way of the predominant flow of metal.
Thin portions of a metal forging are called ribs and webs. A rib is a section that runs perpendicular to the forging plane as determined by the parting line. Long narrow ribs are harder to fill and require more forces, increasing the width of a long rib will better facilitate the filling of the rib with material during the process. A web is a portion of the metal forging that runs parallel to the forging plane. The thickness of webs can be minimized as much as practical. When designing a forging die, web thickness should not be too small or else there may be trouble completely filling the web with metal. Webs that are too thin may also cool faster than the rest of the metal forging, the resulting shrinkage could cause tears or warping of the part.

As the work material fills the die cavity, the flow of metal will have to change directions depending upon the part's geometry. Smooth, large filleted turns will allow the metal flow to change directions while adhering to the die's dimensions. If corners within the metal forging are too sharp then the material may not completely follow the path of those corners, resulting in vacancies, laps, or cold shuts. Sharp corners will also act as stress raisers within the die cavity. Good forging die design should provide adequate enough fillet and corner radius to allow for easy metal flow.
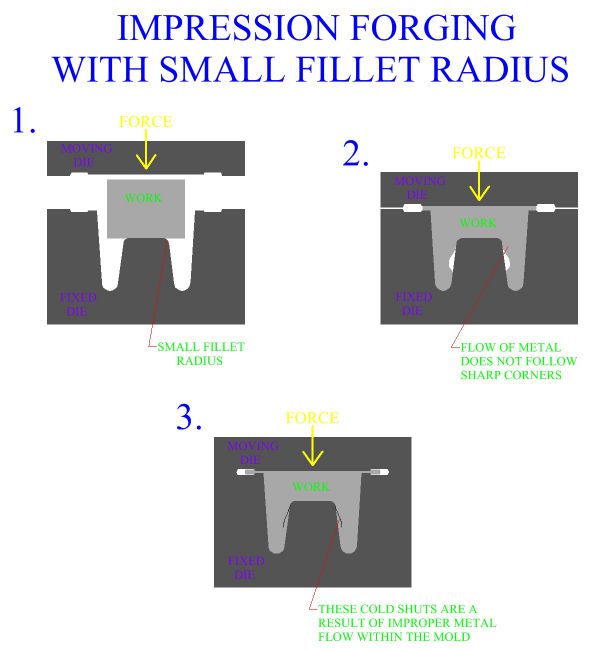
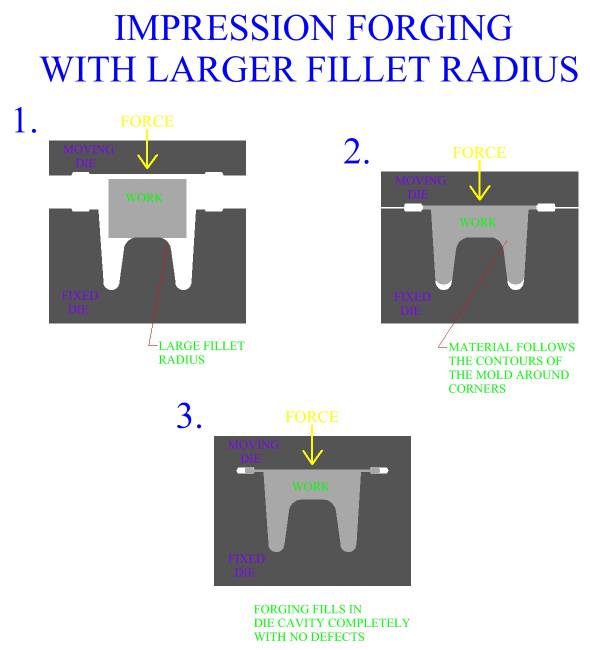
Draft angle, in metal manufacturing processes, is the taper around the internal and external sides of a part. Draft angle is necessary to include in the forging die design in order to allow the removal of the work from the die after the part has been forged. The larger the draft angle, the better it will facilitate the metal forging's removal. As the metal forging cools, it shrinks away from the outer surfaces of the die cavity, therefore exterior draft angles are usually made smaller than interior angles.
In general, easier to forge metals, such as aluminum and magnesium, require less draft angles than harder to forge materials, such as steel, nickel, and titanium alloys. Often in metal forging operations, there is an ejector to help push the part from the die cavity. However, ejectors are not used in drop forging. Draft angle effects the complexity of the forging that may be produced. The greater the draft angle, the more it limits metal forging complexity. Some precision forging operations produce a forged part with no draft angle. Common draft angles used in manufacturing industry are 3, 5, 7, and 10 degrees.
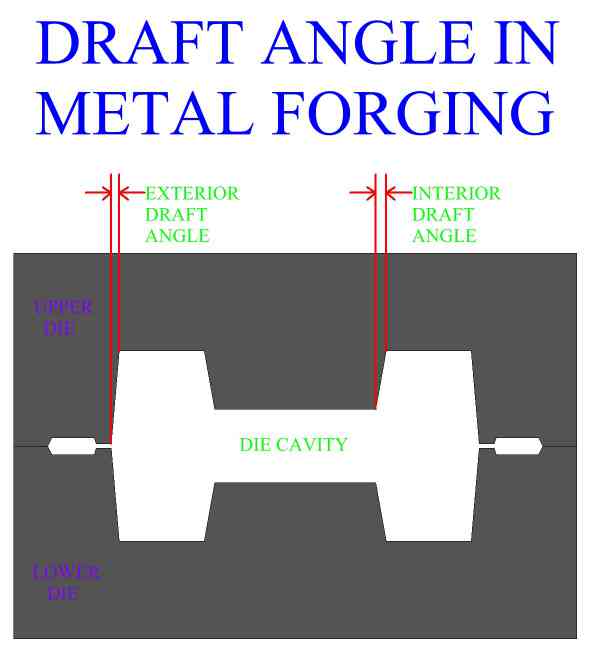
Similar to the pattern in metal casting, the size of the die cavity in metal forging manufacture should account for the size of the part, shrinkage of the part during cooling, and allowances for machining and other finishing operations that may follow the metal forging process.
Location of the parting line is of primary importance in metal forging die design. The parting line, which defines the forging plane of the operation, is a large determinant in how metal flows through the die during the forging's compression. The parting line dictates where flash will be formed, and effects the grain structure of the manufactured part. It is easier to fill sections closer to the parting line than further away. In determining a parting line the maximum periphery of the metal forging should be considered.
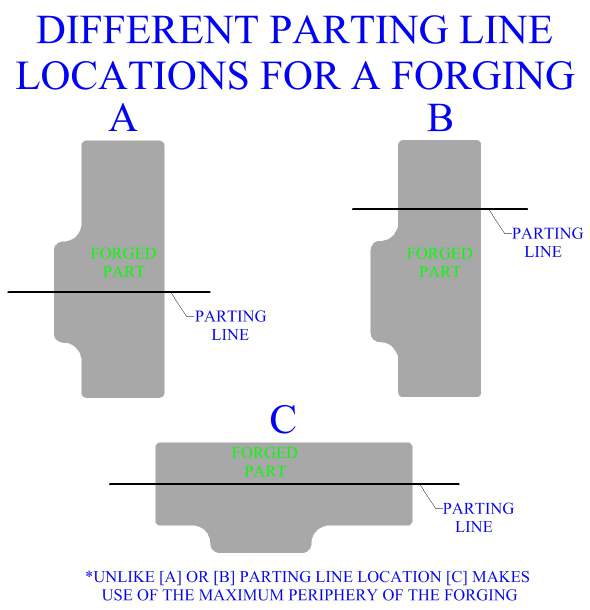
This Figure shows a metal forging with three possible locations for a parting line. The location of the parting line of C will better facilitate the flow of metal through the die cavity, since unlike A or B, location C makes use of the maximum periphery of the forging. It is easier to fill material near the forging plane than in the further recesses of the die cavity. In addition to being a major factor in the flow of metal during the forging process, the location of the parting line is also critical in the formation of the grain structure of the forged work. The parting line acts to disrupt the metal's grain structure.
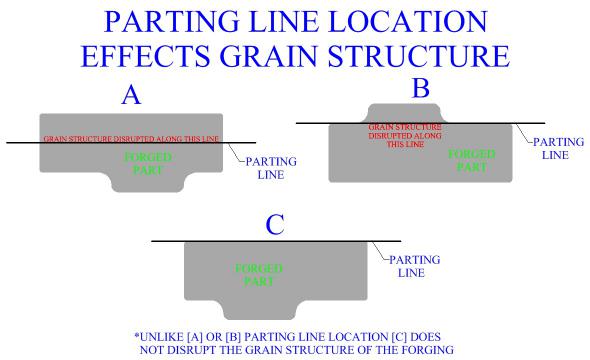
The figure also shows three possible parting line locations for a metal forging. The placement of the parting line in A and B acts to disrupt the grain structure of the metal at the plane through which it passes. Locating the parting line at the top of the forging as in C eliminates the rupture of the forging's grain structure. Also this particular location of the parting line will allow for the entire impression to be formed in one die, while the other die can be flat. Design of the die as in C is both more economical and provides superior grain structure of the metal forging.
Forging Process Design
In modern manufacturing industry, metal parts of complex geometry are often forged completely with the need for only minor finishing operations. These parts can not be manufactured with a single forging. The work stock is taken through a series of metal forging operations that, in steps, alter the geometric shape of the material until the final process creates the desired forging. In these types of design sequences each operation must be planned in such a way as to prepare the work piece for the next forging process. Together the series of metal forging operations that are required to create a part, make a larger single process and each individual forging operation has its place within the larger process.
When designing a complex metal forging process, great consideration should be taken with each step and how it relates to the final product. Also, design the chosen path for the redistribution of the work material from the start of the process to the end of the last step, concentrating on smooth metal flow. Forging design, in general, should first accomplish a rough redistribution of the material, then the more detailed impression die forging operations, and finally finishing operations. In addition to providing a smooth transition of material the forging processes, as a whole, should be designed to produce a controlled grain structure in the final product. When choosing a path for material redistribution, a metal forging design should consider how this particular method of metal deformation will effect and change the grain structure of the part. It is desirable that the final product contain a favorable grain orientation throughout the structure of its material. Such a grain structure should strengthen the part, particularly with respect to that part's application.
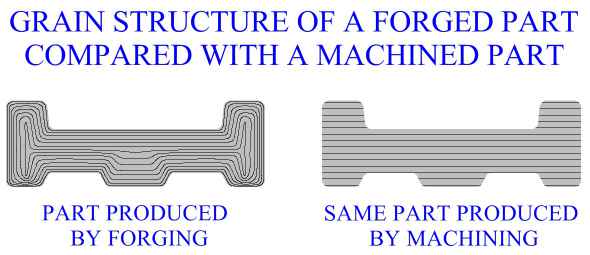
Open die forging often plays a roll in the early stages, providing a general mass redistribution of the work metal. Before the more detailed impression forgings can shape the work, metal must be formed in such a way as to place higher concentrations of material in regions that will require more material. Fullering and edging of the metal, discussed in the open die forging section, are very important open die forging processes used to accomplish a rough transfer of material. Fullering and edging will squeeze more metal into some areas of the work, while causing other areas to have less depending on the needs of the process. Figure 170 shows two rough forms, one was subject to fullering the other to edging, the nature of the different processes should be apparent.
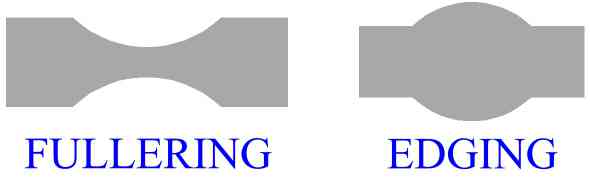
Impression die forging occurs after the rough form has been shaped. This closed die forging process will create the geometric features of the part on the work. The flow of metal must be carefully designed both before and during this phase. Finishing processes, such as sizing, create less but very accurate geometric change to the forging in the final stages of part manufacture. Figure 171 shows the different steps in the metal forging process used to manufacture a complex part.
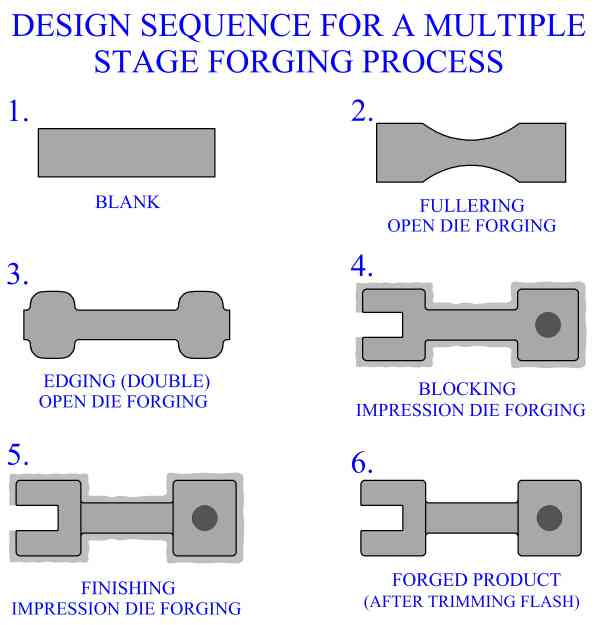
Most industrial metal forging products will be processed by further manufacturing operations that will impart higher tolerances and dimensional accuracy than forging manufacture alone. These operations, (such as machining), although more accurate than forging, do not produce the stronger material of forged metal work. By combining different types of processes such as machining and metal forging, a manufacturer can utilize the benefits of both processes, creating very accurate parts, good surface finish and superior mechanical properties.
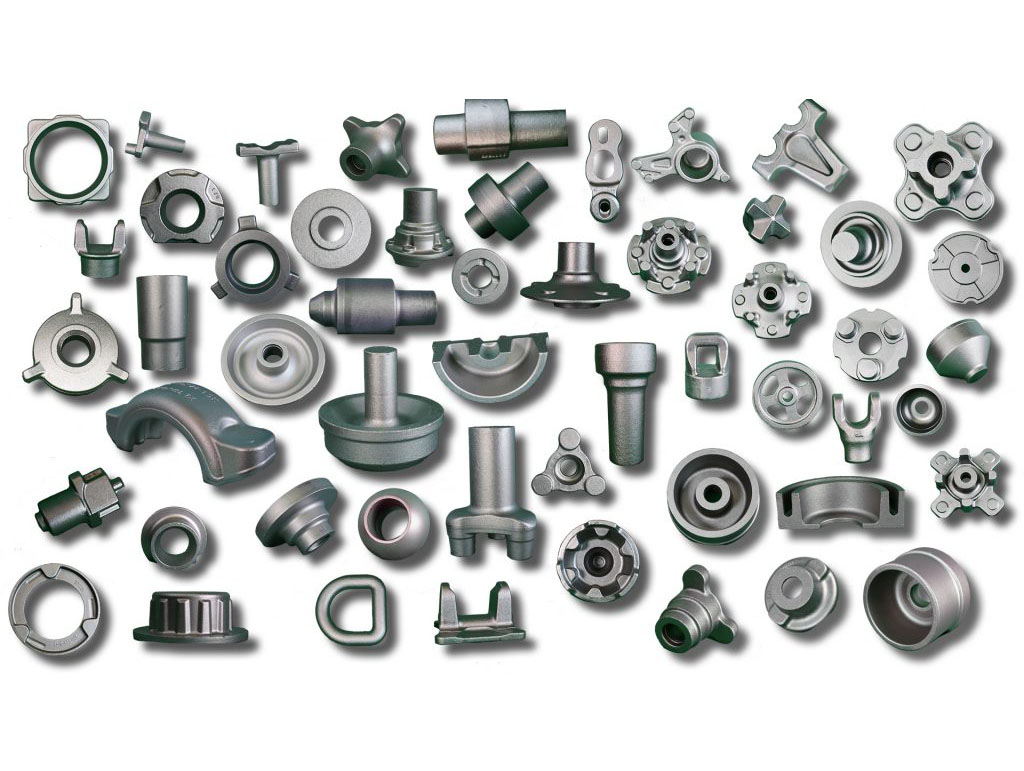