Hydraulic and Mechanical Presses
The press represents a specific type of machine tool, essential in the performance of industrial manufacturing processes. Presses deliver energy through a force that acts over a distance or stroke. One important application is in metal forging manufacture.
Hydraulic and Mechanical Presses
The press represents a specific type of machine tool, essential in the performance of industrial manufacturing processes. Presses deliver energy through a force that acts over a distance or stroke. One important application is in metal forging manufacture. The energy of the press is used to close the die, forging the part within. Press machine tools apply force/energy to the work differently than drop hammers, (that deliver energy to the work through a collision), hammers are the other class of machine tools used to forge metal parts. Drop hammers are covered on the previous page. This page will cover different types of press machines, their function, and capabilities, although it is located in the metal forging section, forging is only one class of manufacturing processes that employ presses.
Press machines are also the primary machine tool used in metal extrusion and sheet metal fabrication processes. Hydraulic and mechanical presses are employed during sheet metal forming to the extent that sheet metal processes, in general, are often referred to as press working. Presses may be used in the manufacture of plastic parts. Machining operations, such as broaching, may also require presses.
Press machine tools vary in size and in the amount of force they can output. The energy from a press is often used to do work requiring a tremendous amount of force, such as a large amount of plastic deformation of a sizable piece of metal. The method and nature by which a press machine will deliver its energy will vary, dependent on its type.
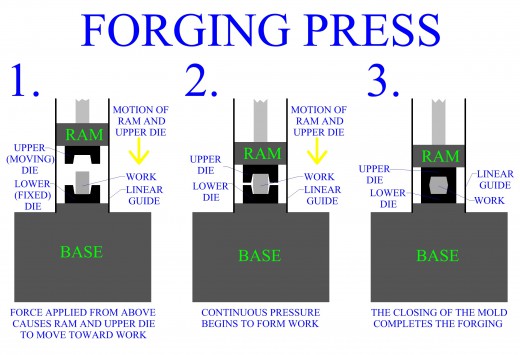
Machine presses shown here are vertical, meaning that the force vector is up and down relative to gravity. In many cases these same machine types are utilized horizontally, meaning the force is delivered in a path perpendicular to the direction of the force of gravity. If the force be exerted vertically, horizontally, or at some intermediate angle, the working principles of each type of machine tool are the same.
Press machine tools are of two main types, hydraulic presses and mechanical presses. Selection of a type of machine press depends on the factors of the manufacturing process. The first consideration would be the basic type of process the press tool will be employed to perform. For example, a press for metal forging, a press for extrusion, a press for impact extrusion, or a press for sheet metal working will all have different general requirements. The next very important factor in machine press selection for a manufacturing operation is the press capacity required. Required press capacity is likely related to the size of the work stock, and type of process. Length of stroke over which the press delivers force is another primary factor when choosing a press machine tool, this also will be related to the basic type of process being employed. These initial considerations should give an immediate idea of the general type of press required. After this, all the specific factors of the manufacturing process should be weighed, to determine the best choice for a press machine tool.
Hydraulic Presses
Hydraulic presses are a powerful class of machine tools, they derive the energy they deliver through hydraulic pressure. Fluid pressure, in a particular chamber, can be increased or decreased by the use of pumps, and valves. Sometimes devices and systems may be used to increase the capacity of the pumps in more powerful presses. These presses can operate over a long distance and at a constant speed. Hydraulic presses are generally slower relative to other press machine types. This involves longer contact with the work, therefore the cooling of the work can be an issue when hot forming a part with hydraulic force. Hydraulic presses are capable of being the most powerful class of presses. Some may be as large as buildings, and can deliver awesome pressure. The largest hydraulic presses are capable of applying 75,000 tons, (150,000,000 lbs), of force. The hydraulic press shown is being used to manufacture a metal forging. Extrusion is also a very common use for such a press, although extrusion is often performed horizontally.
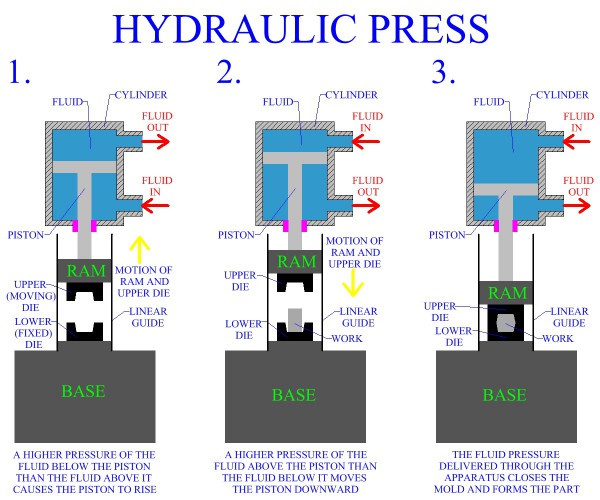
The basic working principles of the hydraulic press are simple, and rely on differences in fluid pressure. Fluid is pumped into the cylinder below the piston, this causes the fluid pressure under the piston to increase. Simultaneously, fluid is pumped out of the top channel, causing the fluid pressure above the piston to decrease. A higher pressure of the fluid below the piston than the fluid above it causes the piston to rise. In the next step, fluid is pumped out from below the piston, causing the pressure under the piston to decrease. Simultaneously, fluid is pumped into the cylinder from the top, this increases the fluid pressure above the piston. A higher pressure of the fluid above the piston, than the fluid below it, moves the piston downward.
Mechanical Presses
Mechanical presses belong to a class of machine tools that encompass a wide range of different machine types. Primarily, the mechanical press transforms the rotational force of a motor into a translational force vector that performs the pressing action. Therefore, the energy in a mechanical press comes from the motor. These types of presses are generally faster than hydraulic or screw presses, (actually the screw press may also be classified as a mechanical press). Unlike some presses, in a mechanical press, the application of force varies in both speed and magnitude throughout the distance of the stroke. When performing a manufacturing operation using a mechanical press, the correct range of the stroke is essential.
Presses are chosen based on the characteristics of the manufacturing process. Mechanical press machine tools are commonly used in metal forging manufacture, and sheet metal working. The desired application of force will dictate the type of machine required. Extrusion will often necessitate a more consistent force over a longer distance. However, a mechanical press may often be a good choice for impact extrusion, since a fast, quickly repeatable application of force over a limited distance is what is needed for that type of manufacturing process. The most powerful mechanical presses in modern manufacturing industry will have a press capacity of about 12,000 tons, (24,000,000 lbs).
Crank Press
The crank press uses a crank link attached to a drive shaft. The crank link rotates with the drive shaft and is attached to a connecting rod by a rotational joint. The connecting rod rocks back and forth during the motion of the crank. The connecting rod is, in turn, attached to a ram by a rotational joint. The ram operates in a slider joint and travels a one dimensional path in both directions. It is through this path that the crank press delivers its force. The crank press does allow for a stoke of a relatively long distance.
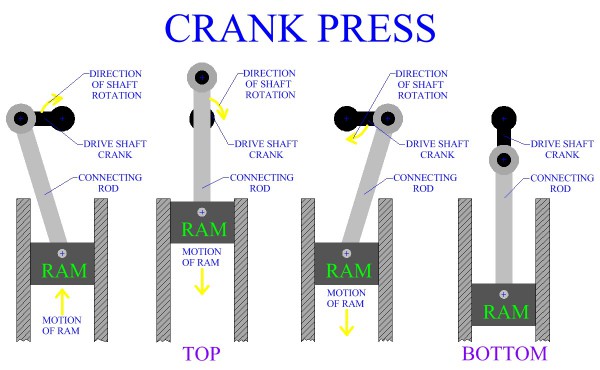
Knuckle Joint Press
The knuckle joint press translates the energy of a motor through a powerful linkage design, and is capable of delivering a tremendous amount of force. The drive shaft crank rotates completely. The links are well grounded to support such pressure.
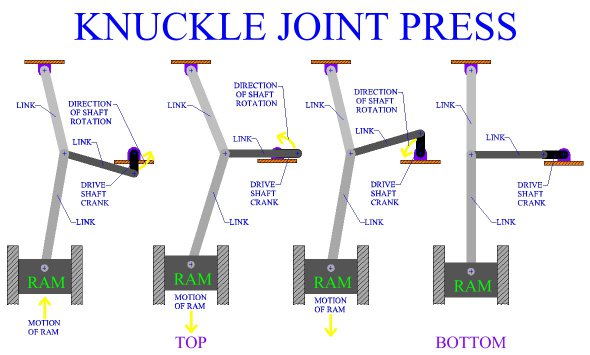
Eccentric Press
The eccentric press uses a motor to drive an eccentric shaft, rotating in a connecting rod. The connecting rod moves a ram in a slider joint one dimensionally. The eccentric shaft itself is round, therefore it may completely rotate within the connecting rod. The center of the drive is not the center of the overall shaft. As the motor rotates, the center of the drive remains stable but the overall center of the shaft changes. This causes the shaft to change position, providing motion. The actual principle of an eccentric press is very similar to a crank press.
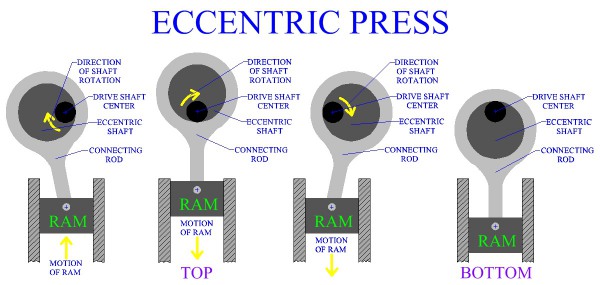
Rack And Pinion Press
The rack and pinion press delivers the motors energy from a gear directly connected to the drive shaft. The rack is actually a round gear of infinite radius. A rotating gear (pinion), provides force through the rack. This gives the one dimensional, translational motion desired of press machines.
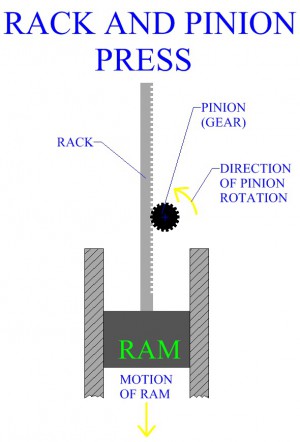
Screw Presses
Screw presses use the rotational energy of a motor to turn a large screw. Typically, a friction disk is used to translate the force from the drive shaft to the screw's head. The screw pushes a ram with great mechanical advantage. Screw presses are similar to hydraulic presses in that they are relatively slow and require a longer contact with the work. Screw presses are also similar to hydraulic presses in that they can produce a constant amount of force over a long stroke. Some screw press machine tools in modern industry can produce 31,000 tons, (62,000,000 lbs), of force.
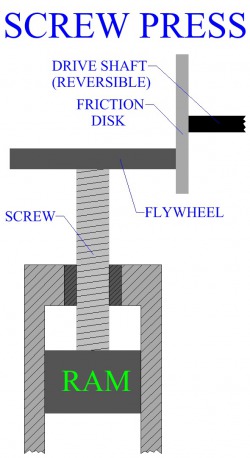
About Forging
Forging Means Uncompromised Strength
Forging is a process, used for adapting the desired shape by the action of hammering or pressing. The materials that are used in this process are generally in the form of ingot, which is produced by the manufacturing companies for applying mechanical operations. Forging is a very old metal working technique, used for shaping. In the early days when there was truancy of advanced digital machines then manual forging operations were done. In those days firstly material being heated in coal furnace then put it on an anvil after that hand-hammering operation done on workpiece to give it a desired shape.
In the current, when machines become more brainy and are able to produce components ranging from a small nut to turbine rotor.
Forging operation is carried out by plastic deformation of the material in between two dies which cross over its mould design on the fed material. There are different type of die frame-up which is gonna use as concern of favourable shape. In the designing of simple product open die forging is adapted but if there is a need for a complex part to be forge, close die technique come into know. This die generally asked for molten metal as feeding material. In open die forging simple hammering operation carried out manually or by machines and shape configuration is obtained.
While working on a closed die, on squeezing the die the same shape which have been Digg on-die prints on the product, the extra material comes out from the die which is removed by the path of peripheral and being trimmed latter.
There are two main types of closed die forging come into know
1. Press forging
2. Drop forging
Press Forging
In press forging material is squeezed between dies very slowly with the use of mechanical press or hydraulic press. Because of its slow operation the final product comes with more dimensional accuracy and fine surface area is received.
Press forging is a method of forming a piece of metal into a specific shape by applying gradual pressure on a shaped die holding the metal. In closed-die press forging, the metal is completely enclosed in a die and pressure is applied on the die. Compared to open-die press forging, closed-die is an overall more efficient method with lower chance of error.
With press forging, the metal is shaped in a uniform way from the surface to the center. This means the impressions created are cleaned and the end product is generally stronger. Tongs are usually not required, and draft angles are not as frequently used. Initial setup costs are also higher with press forging, but the method becomes more cost effective as volume increases.
Compared to drop forging, press forging has the advantage of being more cost effective for higher volume runs, and also results in a stronger workpiece. It also retains the strength benefits of forging compared to casting.

Process of Press Forging:
The forging done with the help of presses is known as press forging. It is usually referred as hot pressing, and is carried out either using hydraulic presses or mechanical (crank type) presses.
The press forging is similar to drop forging but uses a single, continuous, slow squeezing action instead of a series of impact blows. Because of slow ram travel and continuous action of the hydraulic presses, the deformation penetrates deeper so that the entire volume of the work piece simultaneously and uniformly undergoes plastic deformation. While in case of drop forging, the energy is only transmitted into the surface layers of the work part.
A good industrial practice is to use shaped blanks or preforms so that it can be forged in a single continuous stroke. The press forging may be of flash type of fleshless. In flash-press-forging, the surplus metal is flashed out in the gutter, provided at the parting line, while in flashless-press-forging, the entire material is utilized to fill the die cavity.
In both the processes, the forged part is pushed out of the die cavity by means of an ejector, as shown in Fig. 5.22:
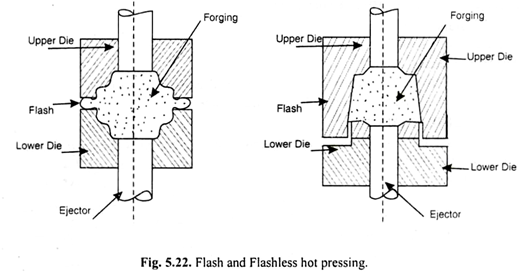
Both, hydraulic presses and mechanical presses are employed for press forging operation. The mechanical presses are used for light work while the hydraulic presses are employed for heavy work. Also, the mechanical press operates faster than the hydraulic presses but provides less squeezing force. Fig. 5.23. Shows the sequence of operation, the estimated die life for production of bearing races.
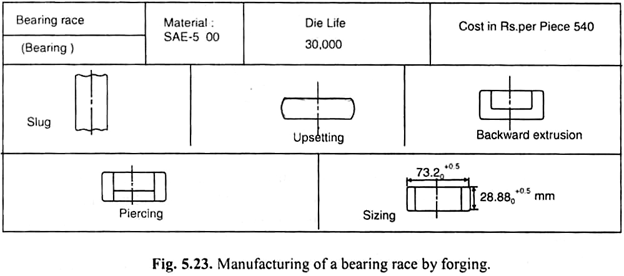
Advantages of Press Forging:
1. Higher productivity than drop forging.
2. Greater accuracy in terms of tolerances within 0.01 to 0.02 inch.
3. Dies used in press forging have less draft, therefore more complicated shapes can be forged with better dimensional accuracy.
4. The speed, pressure and travel of the die are automatically controlled, in press forging.
5. Possibility of process automation through mechanism of blank feeding and forging removal.
6. The operation is completed in a single squeezing action, saves the time.
7. The plastic deformation goes deep into the centre of the work piece, provides uniform and simultaneous deformation throughout the metal.
8. The capacity of presses ranging from 500 to 9000 tons and the number of working strokes per minute can be high as 40 or even 50. Means 40 to 50 parts produced per minute.
9. The press forging, therefore, is suitable for mass production of nuts, bolts, rivets, screws, break levers, bearing races, valves, etc.
Limitations of Press Forging
Nevertheless, the press forging has certain limitations, these are:
1. The initial capital cost is higher compared with drop forging, because the cost of crank press is always higher than that of an equivalent hammer.
2. The difficulty of descaling the blank is another short coming of this process.
3. The process is economically suitable only when the equipment is efficiently utilized.
Drop Forging
In drop forging one material is put into the die and hammering action continues on the die anvil until it takes desired shape. Wrenches, piston and crankshaft are typical example of automobile parts made under forging operation.

Drop forging is a type of closed-die forging. It is used when a large quantity of certain components with sound and good quality forgings are to be produced.
The typical products obtained in drop forging are connecting rod, crank, crank shaft, crane hook, etc. Drop forging process is widely used in automobile industries, airplane parts manufacturing, rail road equipment manufacturing, engine manufacturing industries, agricultural equipment manufacturing industries, etc.

Process of Drop Forging:
The die used in drop forging consists of two halves. The lower half part of die is fastened to the anvil while the upper half part is fixed to the movable ram.
The heated bar or billet is kept in the lower die while the ram delivers four to five strokes (blows) on the metal. When these two die halves come together in closed alignment, the metal spreads and completely fills the die cavity.
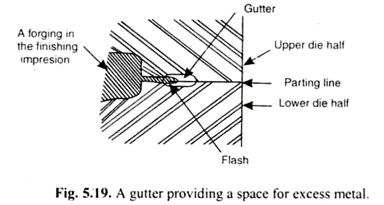
Number of Blows in Drop Forging:
The desired final shape cannot be obtained directly in a single pass or blow. The drop-forging process may involve several blows so that the final shape of the product can be obtained.
The number of blows depends upon the shape of component, desired grain flow direction, the type of metal or alloy being forged.
As many as four passes may be needed while the part is in the ‘Finishing impression’. Also, the part should be slightly lifted between successive blows to prevent over heating of the die.
The numbers of blows when the part is in ‘Pre-shaping impressions’ are two times the number of blows when the part is in ‘Finishing impression’. Lubricants are applied within the die cavity to ensure easy flow of the metal and to reduce friction and die wear.
Finally, the gas pressure is used to force out the part from the die.
Steps in Forging a Connecting Rod:
The sequence of operational steps in drop forging a connecting rod is shown in Fig. 5.20:
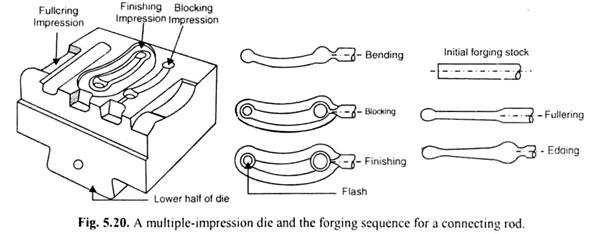
(i) Fullering Impression:
Fullering is a very First step to reduce the stock to the desired size. The fullering operation is done in the fullering impression of the die. The heated stock is first placed in the fullering impression and then hammered once or twice to obtain local spreading of metal on the expanse of its cross section.
(ii) Edging Impression:
The stock is then transferred to the edging impression, where the metal is redistributed along its length in order to properly fill the finishing die cavities. In this process, the exact amount of metal is “Gathered” at certain predetermined cross-sections and reduced at some other ones. The edging is an important step and is usually achieved through a series of blows, together with turnovers of the metal, as required.
(iii) Bending Impression:
The next operation is the bending, which may or may not needed. Depending upon the design and shape of the product. The bending operation may be obtained without bending impression, but then, the grain flow direction will not follow the bend shape and thus resulting poor strength grain flow. Thus, to improve the grain flow, a bending impression in the die is always incorporated.
(iv) Blocking Impression:
The blocking operation is also known as semi-finishing operation. It is a step before finishing operation. Blocking operation contributes to reducing the tool wear in the finishing impression. For complex shapes, more than one blocking impression may be used.
(v) Finishing Impression:
It is the impression where the actual shape is obtained. In this process, the surplus metal will form a flash in the parting line which surrounds the forging.
(vi) Trimming Operation:
Finally, the extra flash present around the forging is trimmed to obtain the desired forging.
Advantages of Drop Forging:
1. Good grain flow is achieved.
2. Faster speed of operation.
3. Good strength of material is obtained.
4. Little or no wastage of material.
Disadvantages of Drop Forging:
1. Die preparation is a costly process.
2. Die impression requires a good skill of work.
3. Die maintenance is costly.
4. Part requires little lifting between successive blow to avoid heating of die.
5. Flash produced must be trimming off to get final shape.
Forging Benefits
Why Forgings are best?
The forging process can create parts that are stronger than those manufactured by any other metalworking process. This is why forgings are almost always used where reliability and human safety are critical.
FORGINGS compared to Castings
Forgings are stronger. Casting cannot obtain the strengthening effects of hot and cold working. Forging surpasses casting in predictable strength properties - producing superior strength that is assured, part to part.
Forging refines defects from cast ingots or continuous cast bar. A casting has neither grain flow nor directional strength and the process cannot prevent formation of certain metallurgical defects. Pre-working forge stock produces a grain flow oriented in directions requiring maximum strength. Dendrite structures, alloy segregation's and like imperfections are refined in forging.
Forgings are more reliable, less costly. Casting defects occur in a variety of forms. Because hot working refines grain pattern and imparts high strength, ductility and resistance properties, forged products are more reliable. And they are manufactured without the added costs for tighter process controls and inspection that are required for casting.
Forgings offer better response to heat treatment. Castings require close control of melting and cooling processes because alloy segregation may occur. This results in non-uniform heat treatment response that can affect straightness of finished parts. Forgings respond more predictably to heat treatment and offer better dimensional stability.
Forgings' flexible, cost-effective production adapts to demand. Some castings, such as special performance castings, require expensive materials and process controls, and longer lead times. Open-die and ring rolling are examples of forging processes that adapt to various production run lengths and enable shortened lead times.
FORGINGS compared to Weldments/Fabrications
Forgings offer production economies, material savings. Welded fabrications are more costly in high volume production runs. In fact, fabricated parts are a traditional source of forging conversions as production volume increases. Initial tooling costs for forging can be absorbed by production volume and material savings and forging's intrinsic production economics lower labor costs, scrap and rework reductions and reduced inspection costs.
Forgings are stronger. Welded structures are not usually free of porosity. Any strength benefit gained from welding or fastening standard rolled products can be lost by poor welding or joining practice. The grain orientation achieved in forging makes stronger parts.
Forgings offer cost-effective designs/inspection. A multiple-component welded assembly cannot match the cost-savings gained form a properly designed, one-piece forging. Such part consolidations can result in considerable cost savings. In addition, weldments require costly inspection procedures, especially for highly stressed components. Forgings do not.
Forgings offer more consistent, better metallurgical properties. Selective heating and non-uniform cooling that occur in welding can yield such undesirable metallurgical properties as inconsistent grain structure. In use, a welded seam may act as a metallurgical notch that can lead to part failure. Forgings have no internal voids that cause unexpected failure under stress or impact.
Forgings offer simplified production. Welding and mechanical fastening require careful selection of joining materials, fastening types and sizes, and close monitoring of tightening practice both of which increase production costs. Forging simplifies production and ensures better quality and consistency part after part.
FORGINGS compared to Machined Bar/Plate
Forgings offer broader size range of desired material grades. Sizes and shapes of products made from steel bar and plate are limited to the dimensions in which these materials are supplied. Often, forging may be the only metalworking process available with certain grades in desired sizes. Forgings can be economically produced in a wide range of sizes from parts whose largest dimension is less than 1 in. to parts weighing more than 450,000 lbs.
Forgings have grain oriented to shape for greater strength. Machined bar and plate may be more susceptible to fatigue and stress corrosion because machining cuts material grain pattern. In most cases, forging yields a grain structure oriented to the part shape, resulting in optimum strength, ductility and resistance to impact and fatigue.
Forgings make better, more economical use of materials. Flame cutting plate is a wasteful process one of several fabricating steps that consumes more material than needed to make such parts as rings or hubs. Even more is lost in subsequent machining.
Forgings yield lower scrap; greater, more cost-effective production. Forgings, especially near-net shapes, make better use of material and generate little scrap. In high-volume production runs, forgings have the decisive cost advantage.
Forgings require fewer secondary operations. As supplied, some grades of bar and plate require additional operations such as turning, grinding and polishing to remove surface irregularities and achieve desired finish, dimensional accuracy, machine-ability and strength. Often, forgings can be put into service without expensive secondary operations.
FORGINGS compared to Powder Metal Parts (P/M)
Forgings are stronger. Low standard mechanical properties (e.g. tensile strength) are typical of P/M parts. The grain flow of a forging ensures strength at critical stress points.
Forgings offer higher integrity. Costly part-density modification or infiltration is required to prevent P/M defects. Both processes add costs. The grain refinement of forged parts assures metal soundness and absence of defects.
Forgings require fewer secondary operations. Special P/M shapes, threads and holes and precision tolerances may require extensive machining. Secondary forging operations can often be reduced to finish machining, hole drilling and other simple steps. The inherent soundness of forgings leads to consistent, excellent machined surface finishes.
Forgings offer greater design flexibility. P/M shapes are limited to those that can be ejected in the pressing direction. Forging allows part designs that are not restricted to shapes in this direction.
Forgings use less costly materials. The starting materials for high-quality P/M parts are usually water atomized, pre-alloyed and annealed powders that cost significantly more per pound than bar steels.
We provide customized forging solutions to our customers, not just commodities. Partner with us and see how our in-house design and engineering expertise delivers real value to you!
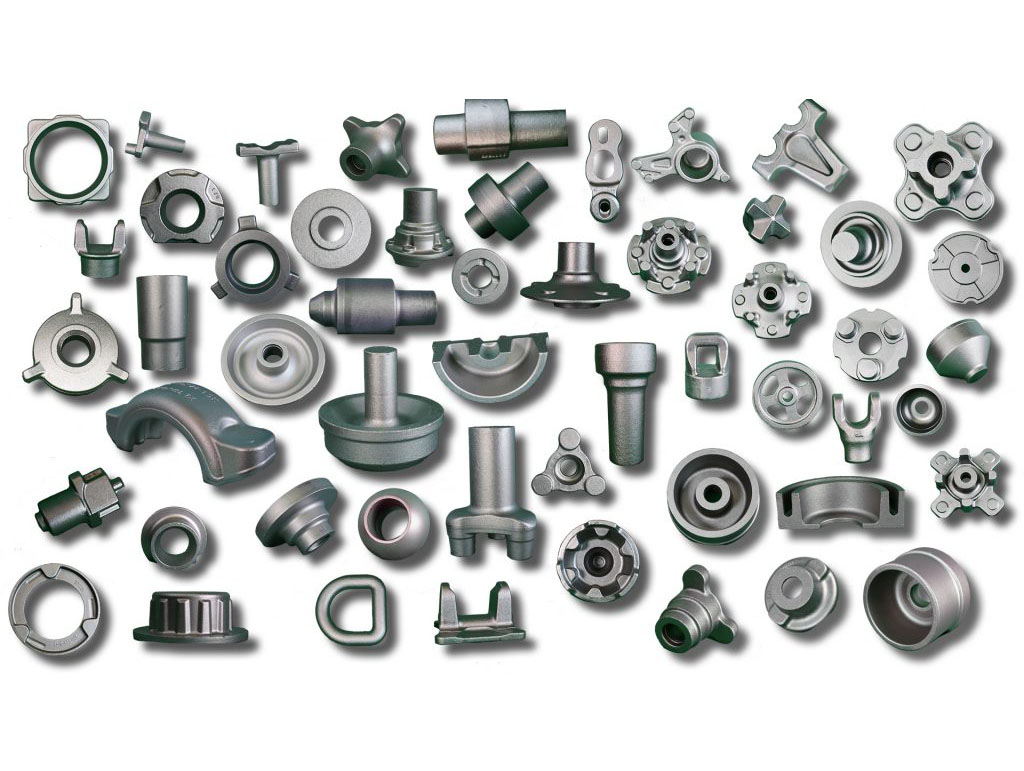