AISI 410 Stainless Steel, SS410(UNS S41000)
AISI 410 stainless steel is one of the most commonly used martensitic stainless steels. It contains about 12% Cr and therefore provides moderate corrosion resistance. Unlike austenite such as AISI 304 and AISI 316, martensite such as grade 410 is magnetic and can be hardened by heat treatment like carbon steel and low alloy steel. SS410 has good tensile strength, creep and fatigue strength and other mechanical properties, mainly used in steam turbines, jet engines and gas turbines.
AISI 410 Stainless Steel Properties, SS410 Heat Treatment, Magnetic, ASTM A276 (SS410)
AISI 410 stainless steel is one of the most commonly used martensitic stainless steels. It contains about 12% Cr and therefore provides moderate corrosion resistance. Unlike austenite such as AISI 304 and AISI 316, martensite such as grade 410 is magnetic and can be hardened by heat treatment like carbon steel and low alloy steel. SS410 has good tensile strength, creep and fatigue strength and other mechanical properties, mainly used in steam turbines, jet engines and gas turbines.
Type 420 is basically a high-carbon version of SS410 which provides higher strength. Ferritic stainless steel 430 contains a higher chromium content, so it has higher corrosion resistance.
Datasheet & Specification
The following tables and lists give the stainless steel 410 datasheet and specification including chemical composition, physical properties and mechanical properties, heat treatment, welding, etc.
Chemical Composition
SS 410 material chemical composition is listed in the following table based on cast analysis.
Datasheet 1, The table below shows AISI 410 stainless steel composition.
Type 410 Chemical Composition, % | ||||||||
ASTM / SAE | AISI (UNS) | C | Si, ≤ | Mn, ≤ | P, ≤ | S, ≤ | Cr | Ni, ≤ |
ASTM A276/A276M | 410 (UNS S41000) | 0.08-0.15 | 1.00 | 1.00 | 0.040 | 0.030 | 11.5-13.5 | – |
ASTM A580/A580M | 0.15, ≤ | 1.00 | 1.00 | 0.04 | 0.03 | 11.5-13.5 | – | |
ASTM A959 | ||||||||
ASTM A479/A479M | ||||||||
ASTM A314 | ||||||||
ASTM A240/A240M | 0.08-0.15 | 1.00 | 1.00 | 0.04 | 0.03 | 11.5-13.5 | 0.75 | |
ASTM A473 | 0.15, ≤ | |||||||
SAE J405 | 0.15, ≤ |
Notes:
- ASTM A276/A276M: Standard Specification for Stainless Steel Bars and Shapes
- ASTM A240/A240M: Chromium and Chromium-Nickel Stainless Steel Plate, Sheet, and Strip for Pressure Vessels and for General Applications
- ASTM A580/A580M: Stainless Steel Wire
- ASTM A479/A479M: Stainless Steel Bars and Shapes for Use in Boilers and Other Pressure Vessels
- ASTM A959: Standard Guide for Specifying Harmonized Standard Grade Compositions for Wrought Stainless Steels
- ASTM A473: Stainless Steel Forgings
- ASTM A314: Standard Specification for Stainless Steel Billets and Bars for Forging
- SAE J405: Chemical Composition of SAE Wrought Stainless Steels
AISI 410 Stainless Steel Properties
The datasheets below list grade 410 stainless steel properties including physical properties and mechanical properties.
Physical Properties
SS 410 stainless steel physical properties are listed in the table below such as density, melting point, specific heat, electrical resistivity, elastic modulus (modulus of elasticity), thermal conductivity, and coefficient of thermal expansion (CTE).
Datasheet 2, AISI 410 stainless steel properties – 1.
Notes:
- 10-6·K-1 = 10-6/K
- 1 Ω·mm²/m = 1 μΩ·m
- 1 g/cm3 = 1 kg/dm3 = 1000 kg/m3
- 1 GPa = 1 kN/mm2
- 1 MPa = 1 N/mm2
SS 410 Physical & Thermal Properties | |
Density, g/cm3 (lb/in3) | 7.9 (0.29) |
Melting point, °C (°F) | 1480-1530 (2700-2790) |
Magnetic permeability | 700-1000 |
Specific heat capacity, J/kg·K (Btu/lb ·°F) | 460 (0.11) at 20 °C (68°F) |
Electrical resistivity, μΩ·m | 0.57 at 20 °C (68°F) |
Elastic modulus (Modulus of elasticity), Gpa (106 psi) | 200 (29.0) |
Young’s modulus, Gpa (106 psi) | 190-210 (27.6-30.4) |
Thermal diffusivity, mm2/s (in2/s) | 6.7 (0.01) at 20 – 100 °C (68 – 212 °F) |
Thermal conductivity, W/m·K (Btu/ft · h ·°F) | 24.9 (14.4) at 100 °C (212 °F) |
28.7 (16.6) at 500 °C (932 °F) | |
Coefficient of thermal expansion, 10-6/K (μin./in. ·°F) | 9.9 (5.5) at 0-100 °C (32-212 °F) |
11.4 (6.3) at 0-315 °C (32-600 °F) | |
11.6 (6.4) at 0-538 ℃ (32-1000 °F) |
Mechanical Properties
AISI 410 stainless steel mechanical properties are given in the datasheet below including tensile strength, yield strength, elongation, reduction in area, Brinell and Rockwell hardness, charpy impact test, etc.
Datasheet 3, Type 410 stainless steel properties – 2.
ASTM A276 Type 410 Mechanical Properties | ||||||
ASTM | AISI (UNS) | Tensile Strength, Mpa (ksi), ≥ | 0.2% Yield Strength, Mpa (ksi), ≥ | Elongation in 2 in. (50 mm) or 4D, ≥ % | Reduction of area, ≥ % | Condition & finish |
ASTM A276/A276M | 410 (UNS S41000) | 480 (70) | 275 (40) | 20 | 45 | A, hot-finished |
480 (70) | 275 (40) | 16 | 45 | A, cold-finished | ||
690 (100) | 550 (80) | 15 | 45 | T, hot-finished | ||
690 (100) | 550 (80) | 12 | 45 | T, cold-finished | ||
830 (120) | 620 (90) | 12 | 40 | H, hot-finished | ||
830 (120) | 620 (90) | 12 | 40 | H, cold-finished |
Mechanical Properties | |||||||
ASTM | AISI (UNS) | Tensile Strength, Mpa (ksi), ≥ | 0.2% Yield Strength, Mpa (ksi), ≥ | Elongation in 2 in. (50 mm) or 4D, ≥ % | Brinell hardness, HBW | Rockwell Hardness | Cold Bend |
ASTM A240/A240M | 410 (UNS S41000) | 450 (65) | 205 (30) | 20 | 217 | 96 HRBW | 180 |
Mechanical Properties | ||||||
ASTM | AISI (UNS) | Tensile Strength, Mpa (ksi), ≥ | 0.2% Yield Strength, Mpa (ksi), ≥ | Elongation in 2 in. (50 mm) or 4D, ≥ % | Reduction of area, ≥ % | Condition & finish |
ASTM A580/A580M | 410 (UNS S41000) | 485 (70) | 275 (40) | 20 | 45 | A, hot-finished |
485 (70) | 275 (40) | 16 | 45 | A, cold-finished | ||
690 (100) | 550 (80) | 12 | 40 | T, cold-finished | ||
830 (120) | 620 (90) | 12 | 40 | H, cold-finished |
Notes for condition:
- A – Annealed.
- H – Hardened and tempered at a relatively low temperature.
- T – Hardened and tempered at a relatively high temperature.
Mechanical Properties | |||||||
ASTM | AISI (UNS) | Tensile Strength, Mpa (ksi), ≥ | 0.2% Yield Strength, Mpa (ksi), ≥ | Elongation in 2 in. (50 mm) or 4D, ≥ % | Reduction of area, ≥ % | Brinell hardness, HBW | Condition |
ASTM A473; A479/A479M |
410 (UNS S41000) | 485 (70) | 275 (40) | 20 | 45 | 223 | Annealed |
485 (70) | 275 (40) | 20 | 45 | 223 | 1 | ||
760 (110) | 585 (85) | 15 | 45 | 269 | 2 | ||
895 (130) | 690 (110) | 12 | 35 | 331 | 3 | ||
Type 410 tempered materials shall be normalized, or liquid quenched from a minimum temperature of 925 °C (1700 °F), and then held at temperature according to condition 1, 2, 3. For each 1 in. (25.4mm) increase in cross section, the time shall be increased by at least 1 hour. |
Mechanical and Impact Properties | |||||||
UNS or AISI type | Charpy V notch impact strength, J (ft·lbf) | Rockwell hardness | Yield strength, 0.2% offset, MPa (ksi), ≥ | Ultimate tensile strength, MPa (ksi), ≥ | Elongation in 50.8 mm (2 in.), % | Reduction of area, ≥ % | Condition |
410 (UNS S41000) | 76 (56) | 43 HRC | 1089 (158) | 1337 (193) | 17 | 62 | Oil quenched from 1010 °C (1850 °F) and tempered at 250 °C (500 °F) |
52 (38) | 26 HRC | 724 (105) | 827 (120) | 20 | 63 | Oil quenched from 1010 °C (1850 °F) and tempered at 593 °C (1100 °F) |
Grade 410 Stainless Steel Heat Treatment
Grade 410 stainless steel heat treatment includes annealing, hardening, tempering and stress relief.
Annealing
Annealing temperature for wrought 410 stainless steel:
- Process (subcritical) annealing: Air cool from temperature 650-760 °C (1200-1400 °F). The maximum softness can be obtained by heating to the temperature at the upper limit of the range. Rockwell hardness: 86-92 HRB.
- Full annealing: Soak thoroughly at a temperature in the range of 830-885 °C (1525-1625 °F); cool the furnace to 790 °C (1455 °F), continue cooling to 595 °C (1100 °F) at a rate of 15-25 °C/h (27-45 °F/h); air cool to room temperature. Rockwell hardness: 75-85 HRB.
- Isothermal annealing: Heat to 830-885 °C (1525-1625 °F); hold 6 h at 705 °C (1300 °F). Rockwell hardness: 85 HRB.
Hardening
Heating to austenitizing temperature 925-1010 °C (1700-1850 °F), the usual time at the temperature range is 30-90 minutes, the quenching agent is air or oil (for parts thicker than 6.4 mm (0.25 in), oil quenching should be used; Martempering baths at 150-400 °C (300-750 °F) can replace oil quenching.);
- Tempering temperature: 205-370 °C (400-700 °F), the final tensile strength is 1105-1515 MPa (160-220 ksi ), Rockwell hardness is 38-47 HRC.
- Tempering temperature: 565-605 °C (1050-1125 °F), the final tensile strength is 760-965 MPa (110-140 ksi ), Rockwell hardness is 25-31 HRC. (Not recommended to temper at the temperature range of 370-565 °C (700-1050 °F), as this will result in lower and unstable impact performance and poor corrosion and stress corrosion resistance.)
Forging
SS410 typical forging temperature range is 900-1200 °C (1650-2200 °F).
Heat Resistance
Maximum service temperatures in air
- Intermittent service: 815 °C (1500 °F)
- Continuous service: 705 °C (1300 °F)
Welding
Martensitic stainless steels are the most difficult stainless steels to weld because their chemical balance makes them harder, stronger, and less ductile during heat treatment. These same metallurgical changes are caused by welding heat.
AISI 410 stainless steel can be welded under annealing, hardening, quenching and tempering conditions, and often produce satisfactory welds without postweld heat treatment, but preheating are required. Usually preheated to 260°C (500°F); Welded at this temperature; Slow cool below 65 °C (150 °F); Temper.
Steels with a high carbon content (such as grade 420 and 440A) usually require post-weld heat treatment.
Filler metal for arc welding | |
Steel | Electrode or welding rod |
410 | E/ER410, E/ER308, E/ER309 |
For arc welding of type 410 stainless steel, the following is recommended (for reference only):
- During the welding process, preheat to 250°C (480°F) and maintain this temperature.
- Use austenite electrodes like AWS E/ER308 or 309. If stronger welding is required, AWS E/ER410 should be used.
- After welding, allow the joint to cool to the preheat temperature, which is 250°C (480°F).
- Before allowing the joint to cool to room temperature, perform tempering at 720°C (1330°F), and for every 1 in. of thickness add, the time increases by at least 1 hour.
- Cool to room temperature.
Applications
Type 410 steel is the basic general-purpose steel used for steam valves, tray valves, pump shafts, turbine blades, bolts and miscellaneous parts that require corrosion resistance and moderate strength up to 540°C (1000°F).
SS 410 Equivalent Material
Grade 410 stainless steel equivalent to Chinese GB, ISO, Japanese JIS, and European EN standard (Germany DIN EN, British BSI…).
Note: DIN 17440 has been replaced by DIN EN 10088-2 and DIN EN 10088-3.
AISI 410 Equivalent Material | |||||||||||||||||||||
US | European | Germany | China | Japan | ISO | Australia | India | Rusia | Korea | ||||||||||||
Standard | Grade (UNS) | Standard | Grade | Standard | Grade (Steel Number) | Standard | Grade (Steel Number) | Standard | Grade | Standard | Grade | Standard | Grade (ISO Number) | Standard | Grade | Standard | Grade | Standard | Grade | Standard | Grade |
AISI; SAE; ASTM |
410 (UNS S41000) | SAE AMS 5504 | 12.5Cr (410) | EN 10088-1; EN 10088-2; EN 10088-3 | X12Cr13 (1.4006) | DIN 17440 | X12Cr13 (1.4006) | GB/T 1220; GB/T 3280 |
1Cr13; 12Cr13 (New designation) |
JIS G4304; JIS G4304; JIS G4305 |
SUS410 | ISO 15510 | X12Cr13 (4006-410-00-I) |
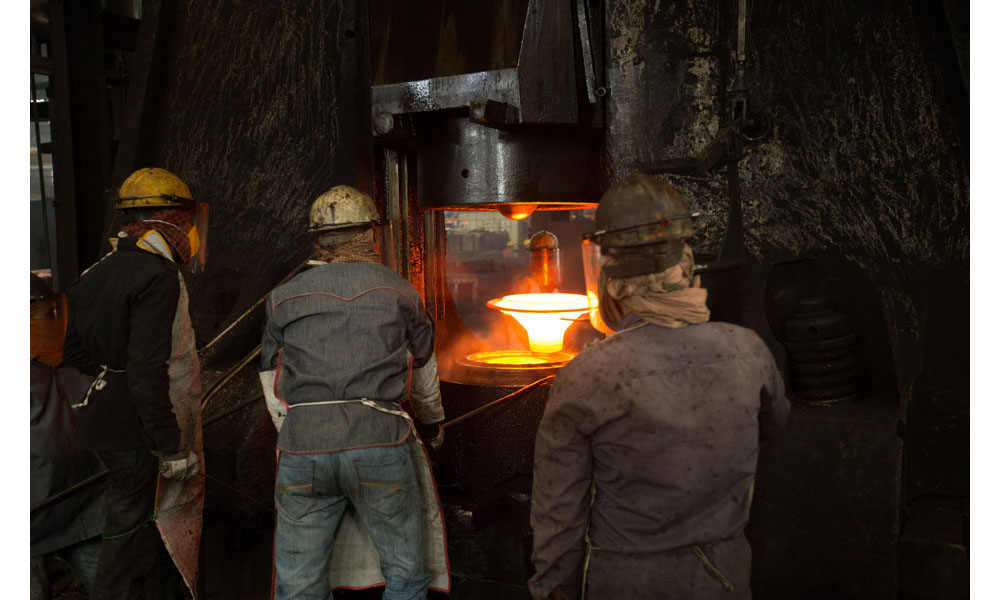