AISI 1070 Carbon Steel (UNS G10700)
Carbon steels are those that have carbon as the specific alloying element. They contain up to 0.4% silicon and 1.2% manganese. The residual elements such as copper, molybdenum, aluminium, chromium and nickel are also present in these steels.
AISI 1070 Carbon Steel (UNS G10700)
Introduction
Carbon steels are those that have carbon as the specific alloying element. They contain up to 0.4% silicon and 1.2% manganese. The residual elements such as copper, molybdenum, aluminium, chromium and nickel are also present in these steels.
The following sections will give an overview of AISI 1070 carbon steel in detail.
Chemical Composition
The chemical composition of AISI 1070 carbon steel is outlined in the following table.
Element | Content (%) |
---|---|
Iron, Fe |
~ 98 |
Carbon, C | 0.65 - 0.75 |
Manganese, Mn | 0.60 - 0.90 |
Sulfur, S | 0.050 (max) |
Phosphorous, P | 0.04 (max) |
Physical Properties
The physical properties of AISI 1070 carbon steel are tabulated below.
Properties | Metric | Imperial |
---|---|---|
Density | 7.7-8.03 g/cm3 | 0.278-0.290 lb/in³ |
Mechanical Properties
The following table shows mechanical properties of cold drawn AISI 1070 carbon steel.
Properties | Metric | Imperial |
---|---|---|
Elastic modulus | 190-210 GPa | 29700-30458 ksi |
Poisson’s ratio | 0.27-0.30 | 0.27-0.30 |
Thermal Properties
The thermal properties of AISI 1070 carbon steel are given in the following table.
Properties | Conditions | ||
---|---|---|---|
T (ºC) | Treatment | ||
Thermal expansion co-efficient | 11.8 x (10-6/ ºC) | 0 - 100 | - |
Other Designations
Other designations that are equivalent to AISI 1070 carbon steel include the following:
- AMS 5115
- AMS 5115C
- ASTM A29 (1070)
- ASTM A510 (1070)
- ASTM A576 (1070)
- ASTM A682 (1070)
- ASTM A713 (1070)
- ASTM A830
- MIL S-11713
- MIL S-12504
- SAE J1397 (1070)
- SAE J403 (1070)
- SAE J412 (1070)
- DIN 1.1231
- SS 1770
- SS 1778
- AFNOR XC 68
APPLICATIONS
- Railroad industry
- Railroad rails
- Street railway rails
- Electric railway wheels
- Heavy machine parts
- Wire
- Hand tools
- Machinery for agricultural use
- Springs
- Mower blades
- Auto industry
- Torsion and stabilizer bars
FORGING
Forge and hot roll form 1800° to 2225°F (982° to 1218°C).
1650°F (899°C) minimum for hot working
Still-air cool
Easily cold drawn when annealed
HEAT TREATMENT
ANNEALING
Anneal by heating to 1550° to 1575°F (843° to 857°C) before air cooling
NORMALIZING
Normalize by heating to 1550° to 1650°F (843° to 899°C) before air cooling
HARDENING
Harden by heating to 1450° to 1525°F (788° to 829°C) before water or oil quenching
TEMPERING
Temper to appropriate strength and hardness, from 400° to 1300°F (204° to 704°C)
May be austempered and martempered
MACHINABILITY
Cobalt high-speed steel or carbide-tip tools
Sulfurized or chlorinated cutting oils for high-speed steel cutters
No oil for carbide-tip tools
Grind high-speed steel turning tools
- 8-12° side rake
- 6-10° back rake
- 7-9° side and end relief
- 12-16° side cutting-edge angle
- 8-14° end cutting-edge angle
- Nose radius 10% of cut depth
Grind carbide-tip tools
- 6-12° side rake
- 2-8° back rake
- 6-10° side and end relief
- 8-12° end cutting-edge angle
- 8-16° side cutting-edge angle
- 1/32” nose radius
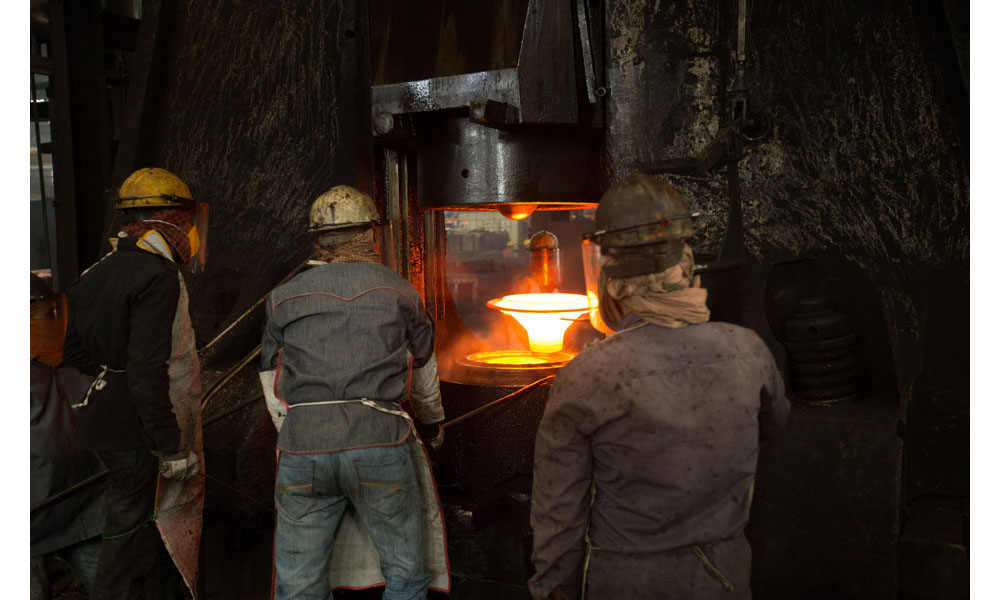