AISI 1055 Carbon Steel (UNS G10550)
Carbon steels are the steels having carbon as the major alloying element. They also contain up to 1.2% manganese and 0.4% silicon. In addition, the residual elements like copper, molybdenum, aluminium, chromium and nickel are present in these steels.
AISI 1055 Carbon Steel (UNS G10550)
Introduction
Carbon steels are the steels having carbon as the major alloying element. They also contain up to 1.2% manganese and 0.4% silicon. In addition, the residual elements like copper, molybdenum, aluminium, chromium and nickel are present in these steels.
The following sections will give an overview of AISI 1055 carbon steel in detail.
Chemical Composition
The chemical composition of AISI 1055 carbon steel is outlined in the following table.
Element | Content (%) |
---|---|
Iron, Fe | 98.41-98.9 |
Manganese, Mn | 0.60-0.90 |
Carbon, C | 0.50-0.60 |
Sulfur, S | ≤ 0.050 |
Phosphorous, P | ≤ 0.040 |
Physical Properties
The physical properties of AISI 1055 carbon steel are tabulated below.
Properties | Metric | Imperial |
---|---|---|
Density | 7.85 g/cm3 | 0.284 lb/in3 |
Mechanical Properties
The following table shows mechanical properties of the cold drawn AISI 1055 carbon steel.
Properties | Metric | Imperial |
---|---|---|
Tensile strength, ultimate | 660 MPa | 95700 psi |
Tensile strength, yield | 560 MPa | 81200 psi |
Modulus of elasticity | 190-210 GPa | 29700-30458 ksi |
Bulk modulus (typical for steel) | 140 GPa | 20300 ksi |
Shear modulus (typical for steel) | 80 GPa | 11600 ksi |
Poissons ratio | 0.27-0.30 | 0.27-0.30 |
Elongation at break (in 50 mm) | 10% | 10% |
Reduction of area | 40% | 40% |
Hardness, Brinell | 197 | 197 |
Hardness, Knoop (converted from Brinell hardness) | 219 | 219 |
Hardness, Rockwell B (converted from Brinell hardness) | 92 | 92 |
Hardness, Rockwell C (converted from Brinell hardness. Value below normal HRC range, for comparison purposes only) | 13 | 13 |
Hardness, Vickers (converted from Brinell hardness) | 207 | 207 |
Machinability (based on AISI 1212 steel. as 100 machinability) | 55 | 55 |
Thermal Properties
The thermal properties of AISI 1055 carbon steel are given in the following table.
Properties | Metric | Imperial |
---|---|---|
Thermal expansion co-efficient | 11 µm/m°C | 6.11 µin/in°F |
Thermal conductivity | 49.8 W/mK | 346 BTU in/hr.ft2.°F |
Other Designations
Other designations that are equivalent to AISI 1055 carbon steel include the following:
- DIN 1.1209
- ASTM A29
- ASTM A510
- ASTM A576
- ASTM A682
- FED QQ-S-700 (1055)
- SAE J403
- SAE J412
- SAE J414
FORGING
AISI 1055 steel is forged between 2200 and 1700ºF (1205 and 925ºC.) After forging the steel could be transferred to a furnace held at roughly the forging finishing temperature, as a preliminary to an annealing cycle.
HEAT TREATMENT
ANNEALING
As mentioned above, forgings may be transferred to a furnace at a temperature that may approximate to the forging finishing temperature. The full annealing cycle of this grade is a soak at a temperature of 1450-1600ºF (790-870ºC) cooling to 1200ºF (650ºC) at 50ºF (28ºC) per hour, soaking and subsequently air cooling.
NORMALIZING
This steel will on occasion require normalizing prior to further heat treatment such as hardening and tempering. This is carried out at a temperature of 1650ºF (900ºC) followed by air cooling.
HARDENING
This steel is austenitized at 1475-1550ºF (800-845ºC) followed by water or oil quench depending upon section size and complexity.
TEMPERING
This steel will be tempered at a temperature to give required mechanical properties, based on past experience. It should be noted that there is a danger of temper brittleness in the temperature range of 500-600ºF (260-315ºC.)
MACHINABILITY
Optimum machinability is obtained from a coarse lamellar pearlite to coarse spheroidite structure.
WELDABILITY
In the event that welding is a requirement, constant preheating and post-weld stress relief should be employed.
Disadvantage of 1055 carbon steel
Although this grade steel has excellent toughness properties they have little or no strain resistance.
With optimum properties in terms of machinability, hardness, and edge retention ability, this steel is considered an idea for kitchen knives. With no corrosion-resistant alloying addition, this steel is prone to rust and may turn black with excessive use.
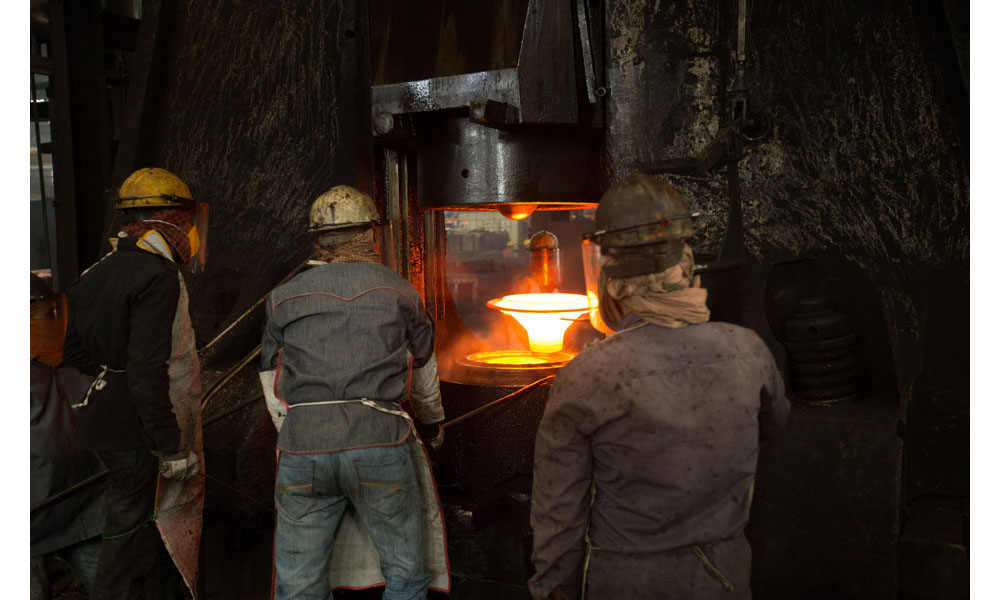