SAE AISI 1018 Steel
SAE AISI 1018 steel is one of the commonly used low carbon steels. It is usually used as carburized steel. Since most of the 1018 carbon steel is produced by cold drawing, this cold rolled steel is called C1018 (1018 cold rolled steel). AISI C1018 steel (1018 CRS) has good weldability, surface hardening quality, higher mechanical properties and better machinability. Cold drawing increases tensile strength, yield strength, torsional strength, surface hardness and wear resistance, but reduces ductility.
SAE AISI 1018 Steel
SAE AISI 1018 steel is one of the commonly used low carbon steels. It is usually used as carburized steel. Since most of the 1018 carbon steel is produced by cold drawing, this cold rolled steel is called C1018 (1018 cold rolled steel). AISI C1018 steel (1018 CRS) has good weldability, surface hardening quality, higher mechanical properties and better machinability. Cold drawing increases tensile strength, yield strength, torsional strength, surface hardness and wear resistance, but reduces ductility.
ASTM AISI SAE 1018 hot rolled steel is also known as 1018 HR, and has good toughness, strength, ductility, formability, weldability and workability.
Applications
AISI SAE ASTM 1018 steel has many semifinished and final products such as round bar, flat bar, steel tubing and pipes, etc.
1018 carbon steel is versatile and is commonly used in a variety of carburized parts such as gears, pinions, ratchets, worms, pins, chain pins, pins, machine parts, tools and mold components.
Forging
C1018 is forged from around 2300ºF down to a temperature in the region of 1650ºF(1260ºC down to 900ºC.). The actual forging and finishing temperatures will depend on a number of factors, including overall reduction during forging and complexity of part being forged. Experience alone will determine near exact values for these two parameters. Parts are air cooled after forging.
Datasheet & Specification
Below is material AISI 1018 carbon steel datasheet including chemical composition, density, thermal expansion coefficient, thermal conductivity, yield strength, hardness, etc.
AISI SAE 1018 Chemical Composition
ASTM AISI SAE 1018 chemical composition is presented in the following table.
AISI SAE 1018 Chemical Composition (%) | ||||
Steel Grade | C | Mn | P (≤) | S (≤) |
1018 (UNS G10180) | 0.15-0.20 | 0.60-0.90 | 0.040 | 0.050 |
AISI SAE 1018 Mechanical Properties
Modulus of elasticity (Young’s modulus): 186 GPa (27×106 psi)
The following tables give AISI SAE 1018 steel mechanical properties of cold-drawn carbon steel rounds, squares, and hexagons.
Steel (UNS) | Tensile strength (Mpa) | Yield strength (Mpa) | Elongation in 50 mm, % | Reduction in area, % | Hardness (HB) | Processing, condition or treatment | Sample Diameter (mm) |
AISI 1018 (G10180) | 483 | 413 | 18 | 40 | 143 | Cold drawn | 16-22 |
440 | 370 | 15 | 40 | 125 | Cold drawn | 20-32 | |
414 | 345 | 15 | 35 | 120 | Cold drawn | 32-51 | |
400 | 220 | 25 | 50 | 115 | Hot rolled (steel bar) | 20-32 |
AISI SAE 1018 Physical Properties
Notes: 10-6/K = 10-6.K-1 = (µm/m)/°C
AISI SAE 1018 mild steel coefficients of linear thermal expansion | ||
Value (10-6/K) | Temperature (°C) | Treatment or condition |
12.0 | 0-100 | Annealed |
13.5 | 0-400 | |
14.5 | 0-600 |
Material 1018 thermal conductivity | ||
Value (W/m·K) | Temperature (°C) | Treatment or condition |
51.9 | 0 | Annealed |
50.8 | 100 | |
48.9 | 200 |
Specific Heat of AISI SAE1018 Carbon Steel | ||
Value (J/Kg·K) | Temperature (°C) | Treatment or condition |
486 | 50-100 | Annealed |
519 | 150-200 | |
599 | 350-400 |
Electrical Resistivity of AISI SAE 1018 Carbon Steel | ||
Value (μΩ·m) | Temperature (°C) | Treatment or condition |
0.16 | 0 | Annealed |
0.22 | 100 | |
0.29 | 200 |
SAE 1018 Steel Heat Treatment
The following table shows AISI SAE ASTM 1018 steel heat treat including annealing, carburizing, carbonitriding, and rockwell hardness.
Full Annealing for Small Steel Forgings
AISI 1018 Steel Heat Treatment | ||||
Heat Treat | Temperature (℃) | Hardness | Cooling/Agent | Section thickness |
Annealing (full annealing of small steel forgings) | 855-900 | 110-150 HB | Furnace cooling (28 °C/h (50 °F/h) | 75 mm |
Heat treatment to 855-900 °C (1575-1650 °F), slow cooling from 855 °C (1575 °F) at a rate of 28 °C (58 °F)/hour to 705 °C (1300 °F), section thickness is less than 75 mm (3 in.)
Typical Heat treatment for SAE 1018 Case Hardening
- Carbon temperature: 900-925 °C (1650-1700 °F), cooling method: water or caustic;
- Reheat temperature: 790 °C (1450 °F), cooling method: water or 3% sodium hydroxide;
- Carbonitriding temperature: 790-900 °C (1450-1650 °F), cooling method: oil;
- Temper temperature: 120-205 °C (250-400 °F), for stress relief and improving resistance to cracking (not mandatory).
Carburizing Treatment
Liquid carburizing in noncyanide baths | |||||||
Grade | Temperature (°C) | Weight (kg) | Case depth (mm) | Time (h) | Quench | Hardness (HRC) | Typical applications |
1018 | 925 | 0.5-2.0 | 0.38 | 0.5-1.0 | Brine | 50-60 | Production tools |
Carbonitriding
Production cycles for carbonitriding | |||||
Grade | Case depth (mm) | Furnace temperature (°C) | Time in furnace | Quench | Applications |
1018 | 0.40-0.50 | 870 | 2 h | Oil at 150 °C (300 °F); tempered at 150 °C (300 °F); for 1 h. | Sliding spur gear, 67 mm outside diameter |
Oil at 150 °C (300 °F); tempered at 260 °C (500 °F) for 1 h. | Spur pinion shaft, 41mm outside diameter |
Welding
The recommended preheat and interpass temperatures for 1018 welding:
For thickness ≤50mm (2 in.), the recommended preheat and interpass temperature is above -12 °C.
For thickness (t) 50< t ≤100, the recommended preheat and interpass temperature is 38 °C (for low hydrogen); and 121 °C (for other than low hydrogen).
Postweld heat treatment is optional, temperature is 590-675 °C (1100-1250 °F).
Equivalent Grade
ASTM AISI SAE1018 carbon steel equivalent to European EN (Germany DIN EN, British BSI, French NF…), Chinese GB and Japanese JIS standard.
AISI 1018 equivalent | |||||||||||
US | Germany | China | Japan | ISO | |||||||
Standard | Grade (UNS) | Standard | Grade | Standard | Grade (Steel Number) | Standard | Grade | Standard | Grade | Standard | Grade |
AISI; SAE; ASTM A29/A29M |
1018 (G10180) | AMS | 5069D |
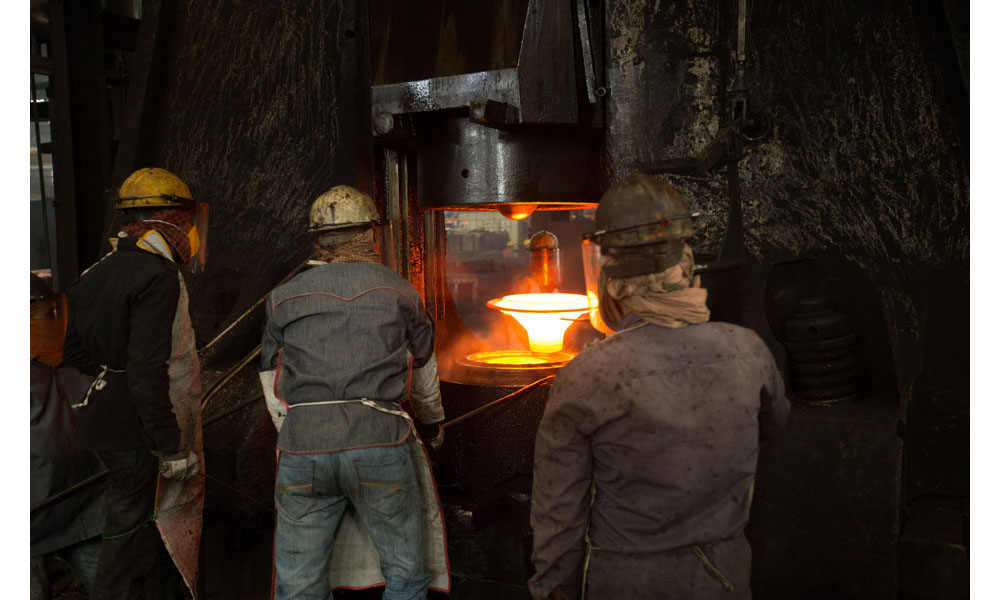