AISI 1015 Carbon Steel (UNS G10150)
Steels with only carbon as their specific alloying element are known as carbon steels. Traces of 0.4% silicon and 1.2% manganese can be found in these steels. Carbon steels also contain small quantities of copper, nickel, molybdenum, aluminium and chromium.
AISI 1015 Carbon Steel (UNS G10150)
Introduction
Steels with only carbon as their specific alloying element are known as carbon steels. Traces of 0.4% silicon and 1.2% manganese can be found in these steels. Carbon steels also contain small quantities of copper, nickel, molybdenum, aluminium and chromium.
The following datasheet provides an overview of AISI 1015 carbon steel.
Chemical Composition
The chemical composition of AISI 1015 carbon steel is outlined in the following table.
Element | Content (%) |
---|---|
Iron, Fe | 99.13-99.57 |
Carbon, C | 0.13-0.18 |
Manganese, Mn | 0.30-0.60 |
Sulfur, S | ≤ 0.050 |
Phosphorous, P | ≤ 0.040 |
Physical Properties
The following table shows the physical properties of AISI 1015 carbon steel.
Properties | Metric | Imperial |
---|---|---|
Density | 7.87 g/cc | 0.284 lb/in³ |
Mechanical Properties
The mechanical properties of the cold drawn AISI 1015 carbon steel are displayed in the following table.
Properties | Metric | Imperial |
---|---|---|
Tensile strength | 385 MPa | 55800 psi |
Yield strength | 325 MPa | 47100 psi |
Bulk modulus (typical for steel) | 140 GPa | 20300 ksi |
Shear modulus (typical for steel) | 80.0 GPa | 11600 ksi |
Elastic modulus | 190-210 GPa | 27557-30458 ksi |
Poisson's ratio | 0.27-0.30 | 0.27-0.30 |
Elongation at break (In 50 mm) | 18.00% | 18.00% |
Reduction of area | 40.00% | 40.00% |
Hardness, Brinell | 111 | 111 |
Hardness, Knoop (converted from Brinell hardness) | 129 | 129 |
Hardness, Rockwell B (converted from Brinell hardness) | 64 | 64 |
Hardness, Vickers (converted from Brinell hardness) | 115 | 115 |
Machinability (based on AISI 1212 steel as 100 machinability. The machinability of Group I bar, rod, and wire products can be improved by cold drawing.) | 60 | 60 |
Thermal Properties
The thermal properties of AISI 1015 carbon steel are given in the following table.
Properties | Metric | Imperial |
---|---|---|
Thermal expansion co-efficient (@0.000-100°C/32.0-212°F) | 11.9 µm/m°C | 6.61 µin/in°F |
Thermal conductivity (estimated based on similar materials) | 51.9 W/mK | 360 BTU in/hr.ft².°F |
Other Designations
Equivalent materials to AISI 1015 carbon steel are listed in the following table.
AMS 5060 | ASTM A29 | ASTM A510 | ASTM A512 (1015, MT 1015) | ASTM A830 |
ASTM A519 (1015, MT 1015) | ASTM A545 | ASTM A549 (1015) | ASTM A575 (M1015) | ASTM A576 |
ASTM A635 | ASTM A659 (1015) | ASTM A787 (MT 1015) | ASTM A794 | ASTM A513 (MT 1015) |
SAE J1397 | SAE J403 | SAE J412 | SAE J414 | ASTM A108 |
FED QQ-S-698 (C1015) | MIL SPEC MJL-S-16974 |
Applications
AISI 1015 carbon steel can be used in forged, cold-headed or cold-formed parts which are low strength with wear resistant and hard surfaces.
FORGING
These grades would be forged from a start temperature in the order of 2300ºF (1260ºC) down to a temperature around 1650ºF (900ºC.) Forging temperatures used will be in many instances based on past experience, and will always take into account the amount of reduction and the complexity of the part being forged.
HEAT TREATMENT
Steels at this level of carbon content, in fact steels with 0.05 up to around 0.25 percent carbon, are used in the as-forged condition. Such forgings show good machinability and little is gained in the way of strength by heat treatment. It is often noted that as-forged strength and machinability at this carbon level are slightly better than are obtained from the normalized condition.
Normalizing may be carried out prior to case hardening, at around 1700ºF (925ºC) or in the event of variations in microstructure resulting from forging of a complex shape.
Other heat treatment for these steels will involve carburizing or other surface hardening treatments, followed by hardening from a temperature in the region of 1400-1450ºF (760 -790ºC.) Large parts of simple shape will be water quenched, all others oil quenched.
TEMPERING
A tempering treatment at 340-410ºF (170-210ºC,) which more or less amounts to a stress relief, may be carried out following hardening. Any further temperatures, to achieve required properties, will be based upon experience.
MACHINABILITY
Good machinability is obtained on these grades in the as-forged or normalized conditions, as described above.
WELDABILIT
Welding of these grades may be carried out by all normal fusion methods, preferably using low-carbon electrodes.
AISI 1015 is a low-carbon steel that offers superior workability and machinability. A versatile engineering and machinery alloy, AISI 1015 is used normalized, hot-rolled, cold-worked or annealed.
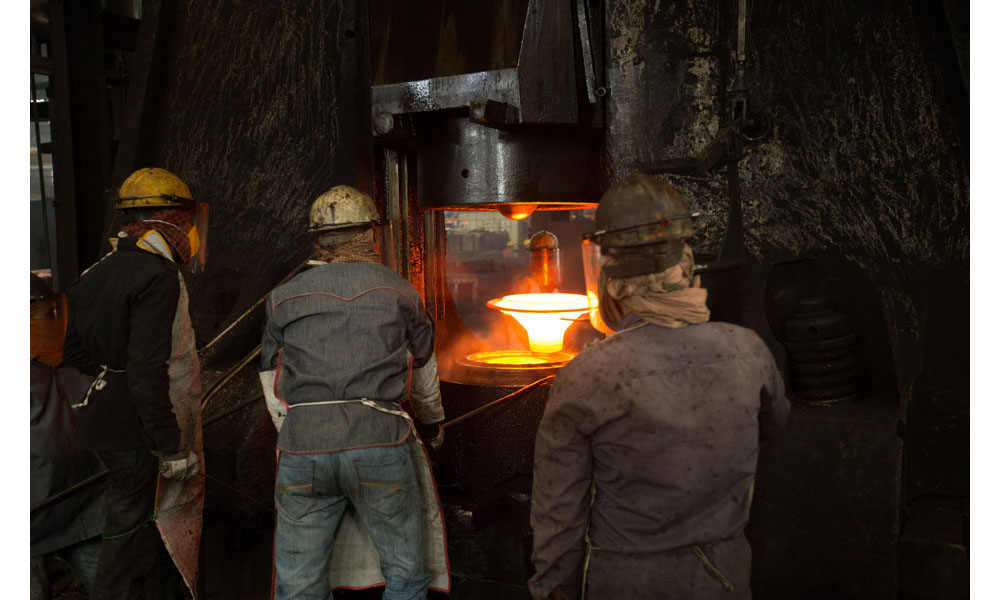